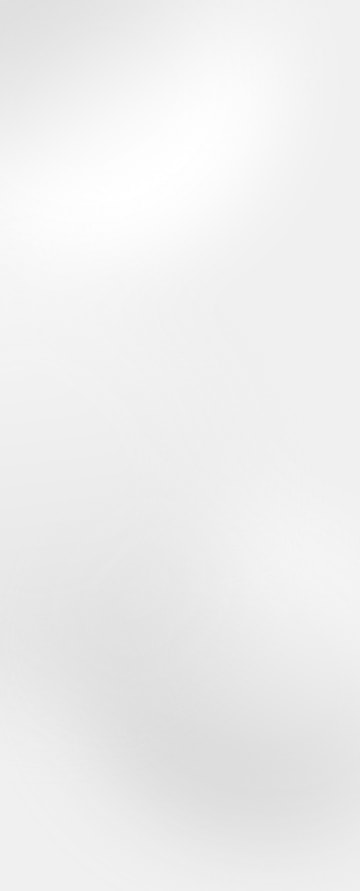
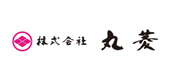
株式会社 丸菱
データ抽出から、帳票作成、出力、封入・封かんまで、
請求書発行プロセスの自動化による業務効率化・スピードアップを実現
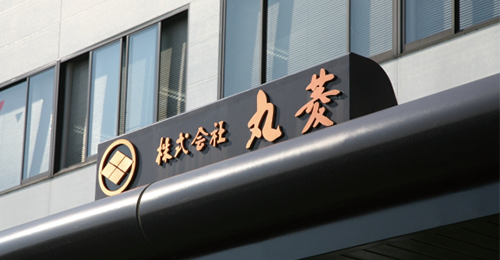
- 業種
-
食料品
製菓・製パン、ホテル、レストランなどに向けた原材料や厨房器具の販売を 主事業とする株式会社丸菱。日々大量の帳票を処理している中で課題と なっていたのが、毎月3,000通を超えて発行する請求書に関する作業負担 の重さだった。この課題を解決すべく丸菱は、SVFを導入することで帳票 システムを全面的に刷新。理想科学工業の高速カラープリンター「オルフィ ・スEX」との連携により、IBM i上で稼働する基幹システムからのデータ抽出 変換、帳票作成、プリンター出力、封入・封かんまで、すべてのプロセスを一 。気通貫で自動化し、業務の大幅な効率化とスピードアップを実現
導入背景
「請求書を送付できる体裁に仕上げるまでには、IBM iで稼働している基幹システムからデータを抽出し、PC上のMicrosoft Accessで帳票を作成し、プリンターで出力し、封かん機に人手で持ち運んで折りや封入・封かんを行うという作業を経ていました。担当者2人が4時間以上も付きっきりになることもありました」
- 課題
-
- 営業品目は数万点、顧客が約5,000店舗に広がり、大量の帳票を処理する必要があった
- 月間3,000通を超える請求書について、顧客に送付できる体裁に仕上げるまでに多大な工数を費やしていた
- 解決策導入ポイント
-
- SVF for System i を利用することで、IBM i(AS/400)で稼働している基幹システムからのデータ抽出・変換、帳票作成、プリンター出力まで、一連の処理を同じサーバー上で実行
- SVF for System iと高速カラープリンター「オルフィスEX」を連携させることで、封入・封かん作業まで一気通貫の自動化を実現
- 効果
-
- 請求書発行に関するトータル作業時間を1/3に短縮し、封入ミスなどのヒューマンエラーも削減
- 手作業で行っていた社判の押印も帳票作成の段階で自動化
- SVFと各営業拠点やグループ会社の複合機をネットワークで連携させることで、電子データでの帳票の受け渡しを実現(予定)
「SVF for System iと高速カラープリンター「オルフィスEX」の連携により、請求書の作成から社判の押印、印刷、封入・封かんまで、すべてのプロセスを自動化。トータルの作業時間を1/3に短縮するとともに、封入ミスなどのヒューマンエラーも削減することができました」
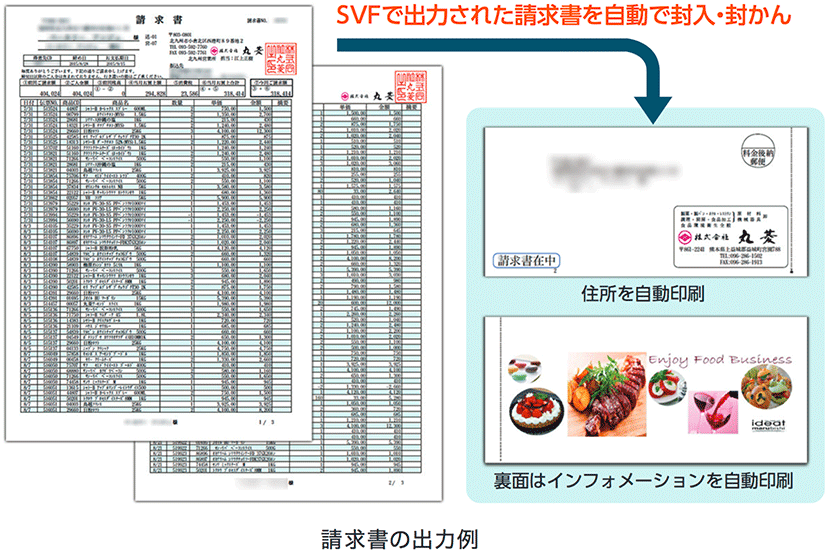
顧客は約5,000店舗に広がり、毎月3,000通を超える請求書を発行
食品分野の総合商社として製菓・製パン、ホテル、レストランなどへの原材料や設備機器の卸を主な事業とする丸菱は、本社のある熊本県を中心に九州一円および山口県に営業展開している。取り扱う営業品目は数万点(登録件数)に達し、顧客は約5,000店舗に広がっている。
さらに近年では、「食品産業のパイプ役、繁栄の使徒」となるという企業理念のもと、店舗づくりや厨房の設計・設備販売、その他アドバイス支援に乗り出すほか、韓国、中国、マレーシアに現地法人を設立するなどグローバル化への取り組みも積極的だ。
このビジネスで欠かせないのが帳票であり、丸菱では月末月初に大量の帳票を作成している。請求書を例に取ると、発行数は月間3,000通を超える。特に取引量の多い顧客に送付する請求書では、明細を添付して30枚以上になることもある。
月次報告など社内向けの帳票も大量で、月末には3~4箱分のプリンター用紙が瞬く間に消費されていくという。丸菱 情報システム部の課長を務める竹下芳広氏は、「総勘定元帳をはじめ電子帳簿保存法に基づいた電子化にも注力しています。同時に、お客様への送付が必要な請求書は紙の出力でニーズにあわせた対応を取り組んでいます。現在紙ベースで保管している月報などの帳票に対し、SVF活用による電子化(資料のPDF保管)や、処理の自動化(請求書の出力から自動封かん)を目指しています。
SVFとオルフィスEXを連携させ、請求書発行のプロセスを自動化する
紙の帳票をなくすことができない以上、その作成から発行までの一連の作業をいかに省力化し、スピードアップできるかが請求書を担当する部門や現場担当者の課題であった。
中でも問題だったのが、前述した請求書にまつわる作業だ。顧客に送付できる体裁に仕上げるまでには、IBM i(AS/400)で稼働している基幹システムからデータを抽出し、PC上のMicrosoft Accessで帳票を作成し、プリンターで出力し、封かん機に持ち運んで折りや封入・封かんを行うというプロセスを経なければならない。「特に封かん機に用紙を移す過程は手作業となるため、財務部の担当者2人が4時間以上も付きっきりになることがありました」と竹下氏は振り返る。
このような非効率を解消し、よりスムーズな帳票出力を実現すべく、丸菱が2014年3月頃から検討を進めてきたのが、SVF for System iによる帳票システムの刷新である。
「IBM iの更新を迎えていた時期に、タイミングよく以前よりシステム構築を依頼していたベル・データ株式会社から帳票ツール『SVF』の提案を受けたのです。データ抽出・変換から帳票作成、プリンター出力まで、一連のプロセスを同じサーバー上で実行できると聞き、大きなメリットを感じました」と竹下氏は語る。
同じ頃、あるイベント会場で偶然に目に止まったのが、理想科学工業の高速カラープリンターである。オプション装置を追加することで、印刷のみならず封入・封かんまで連続処理することができるオルフィスEXというモデルだ。丸菱情報システム部の主任である岡本章氏は、このように語る。
「SVF for System iとオルフィスEXを連携させれば、請求書の作成から出力、封入・封かんまで、すべてのプロセスを一気通貫で自動化できることになります。それは私たちが望んでいた、帳票業務の効率化のあり方そのものでした」
社判の押印もSVFで自動処理し、トータルの作業時間を1/3に短縮
メーカーを問わず幅広いプリンターに対応していることがSVFの特長のひとつだ。もともとウイングアーク1stのアライアンスパートナーである理想科学工業のオルフィスEXについても、もちろん問題なく接続することができる。
ただ、今回の帳票システム導入は全面的な基盤刷新となるだけに慎重にならざるを得ない。丸菱はウイングアーク1stと理想科学工業のサポートを受けながら、基幹システムとSVF、プリンター間の接続を徹底的に検証。確証を得た上で2014年11月にSVF for System iならびにオルフィスEXの導入を正式決定。その後の導入作業やシステム構築、財務部のユーザーを中心とする社内のトレーニングを経て、2015年5月より新帳票システムが稼働を開始した。
「IBM iとSVFサーバーの連携では、基幹システムから必要なデータをワークファイルに切り出してCSV形式に変換しFTP転送するという、当初考えていた以上に複雑な作り込みが必要でした。しかし、ウイングアーク1stのサービス部門のサポートにより、予定どおりに新帳票システムをカットオーバーすることができました」と岡本氏は評価する。
この結果として、請求書発行にまつわる作業負荷は以前と比べ大幅に軽減された。
「一連のプロセスが連続して流れるようになったことに加え、従来は手作業で押印していた社判をSVFによる自動処理で入れるなど効率化を図ったことで、トータルの作業時間を1/3に短縮することができました。また、封入ミスなどのヒューマンエラーの削減でも効果を上げています」と竹下氏は語る。
見積書や複写伝票などあらゆる帳票をSVFに一元化したい
今後に向けて丸菱では、請求書以外の帳票についても順次自動化を進めていく考えだ。
「あらゆる帳票データを集約し、SVFからすべてをコントロールすることで、業務をさらに効率化できると考えています。すでに見積書の自動化を目指した取り組みに着手しているほか、別ソフトで処理している専用帳票(複写伝票)についても、SVFでできないかと検討しているところです」と岡本氏は語る。
また、社内向けの帳票についても常に紙に出力するのではなく、可能な限り電子データの状態で各部門と受け渡しを行う形に改めていく計画だという。
「具体的には、各営業拠点やグループ会社に設置されている複合機と本社のSVFを、インターネットVPNなどで連携させたいと考えています。これにより各オフィスでは、複合機とLAN接続されたPCの画面上で帳票を確認し、必要なものだけを印刷するといった業務の合理化・効率化が可能となります」
さらにその先では、営業や店舗通販などの現場でのデータ分析を可能とする、ユーザー自身による自由度の高い帳票作成を視野に入れており、「BI(ビジネスインテリジェンス)の基盤として、Dr.Sum EAの導入も検討しています」と竹下氏は語る。
今回の帳票システムの刷新をきっかけとして、丸菱はオンリーワンの付加価値提案を目指すビジネスの機動力と対応力を、さらに高めていくに違いない。
Company Profile
株式会社 丸菱
創業 :1951年
所在地 :熊本県上益城郡益城町
事業内容 :製菓・製パン・ホテル・レストランへの原材料や器具の販売、パッケージデザインの提案、衛生管理のサポート、店舗や厨房の設計・設備の販売。
URL :http://www.marubishi-group.co.jp/
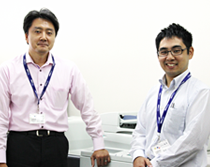
情報システム部 課長 竹下 芳広 氏(写真左)
情報システム部 主任 岡本 章 氏(写真右)
導入製品
SVF
基幹・業務システムからの帳票出力を最適化する帳票基盤ソリューション。柔軟な帳票レイアウトの設計や各社プリンター印刷、多様な出力形式での帳票運用を実現。
SVFソリューションサービス
SVF/RDE製品の新規導入、バージョンアップ時の各種支援サービスをご提供。コンサルティングサービスも実施。