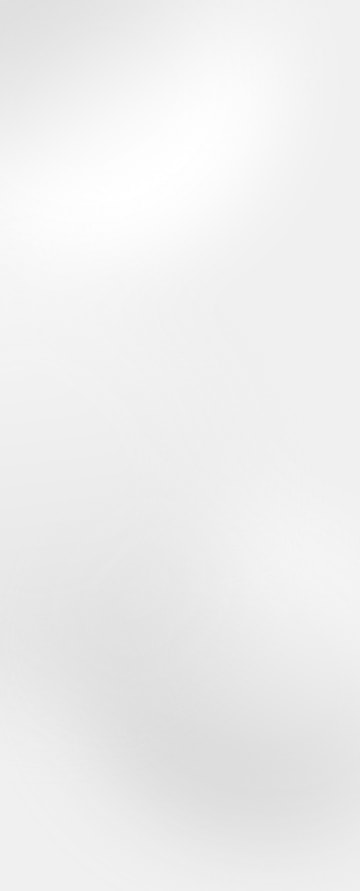
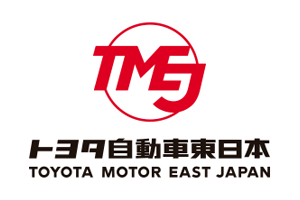
トヨタ自動車東日本株式会社
管理帳票・分析業務のデジタル化で高い品質と生産性向上を両立
製造現場の紙と手書きからの脱却で、DX推進加速を目指す
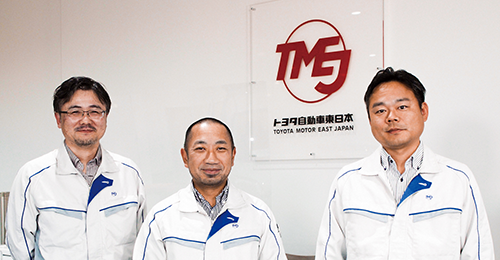
- 製品
トヨタ自動車東日本株式会社(以下、トヨタ自動車東日本)は、製造現場の管理帳票・分析業務における紙と手書き対応のデジタル化を目指し、MotionBoardを採用。着実な改善効果を重ね、管理業務にもその利用を拡大している。同社の品質管理や改善活動文化との親和性も高いMotionBoardによって、DX推進のさらなる加速を目指している。
導入背景
自動車の製造工程におけるさまざまなデータ活用が紙と手書きで行われており、効率化が求められていた。そこで帳票デジタル化と見える化ツールの活用により、自動化による業務効率化を推進。さらなる生産品質の向上を目指した。
- 課題
-
- 部位・工程ごとに数千種類の管理帳票が存在。その多くが手書きでの対応のため、業務負荷が高い
- センサーで取得したデータの傾向分析が、手作業では時間と手間がかかり過ぎて有効活用できない
- 生産計画と実績の管理も紙による記録・掲示のため、タイムリーな情報共有に多大な工数がかかる
- 解決策導入ポイント
-
- i-ReporterとMotionBoardを連携させ帳票入力からグラフ描画、異常傾向のアラート表示までを自動化
- センサー入力の測色管理データベースとMotionBoardを連携。車種、塗色ごとの傾向グラフを自動表示
- 基幹システムや生産設備と連携し実績を自動入力、MotionBoardで可視化。現場改善に必要なデータのスピーディな把握が可能に
- 効果
-
- 手書き起票やグラフ描画の自動化により、多くの人員に対して高い業務改善効果が得られた
- 確実な測色管理により不良の兆候を捉え、未然防止に貢献
- 製造現場の管理者がタイムリーに状況が把握しやすくなり、トラブルを未然に防止できる
- デジタル化により社内にデータ活用が浸透。さらなる使いこなしでDX推進の加速に期待
製造現場における手書き業務の高負荷が課題
トヨタ自動車東日本は、トヨタグループ内におけるコンパクトカーづくりの専門集団として、2012年に設立。「ものづくりを通じて、豊かな社会づくりに貢献する」というトヨタ創業以来の理念のもと、東北を基盤に地域と一体になり、高い技能と技術力をもってより環境にやさしい、より安全なクルマを目指し、日々ものづくりに取り組んでいる。主な生産車種はヤリス、アクア、シエンタなどで、2023年からはレクサスブランドの「LBX」の生産も担当している。
同社がMotionBoardを導入したのは、工場IoTのかけ声が高まり始めた2016年。同社は当時、製造現場におけるデータ活用で、さまざまな課題を抱えていた。
1つ目は、数千種類にも上る、手書きの管理帳票による業務負荷。自動車の製造には、組立や塗装など多くの工程がある。多くの部位や工程ごとに満たすべき基準値があり、その適合が帳票で管理される。同社ではこの帳票業務の多くが紙による手書きで行われており、効率化が求められていた。
2つ目は、塗装品質の管理。バンパーは樹脂、ボデーは鉄板という素材の違いや、実際に塗装を行う工程も異なる上に、気温や湿度などの条件で発色の差異が出ることがある。組立した時に微妙に色が異なるといったことがないように、同社は塗装段階でセンサーを用いて発色を計測、基準値との合否測定を行っているが、手作業では測色結果をグラフ化し、傾向分析することに時間がかかるという課題があった。
情報システム部 インフラグループ グループ長の菅原 吉規氏は、当時の課題を次のように話す。「管理帳票業務では、当時は毎日、人が測り、計算して、グラフ化も手書きで行っていました。たとえば組立工程では、シートベルトなどの安全に関わる箇所は締め付けトルクの検査を行い、基準値通りであるというエビデンスを残すことも求められます。そして記録した数値を基に、傾向分析を行うのですが、多くは紙による手作業で行われていました。塗装工程の測色管理も、データはセンサーで取得できていますが、傾向分析が手作業では時間と手間がかかり過ぎて、追い付かない。これらを何とか自動化、効率化できないかというのが、当時の課題でした」
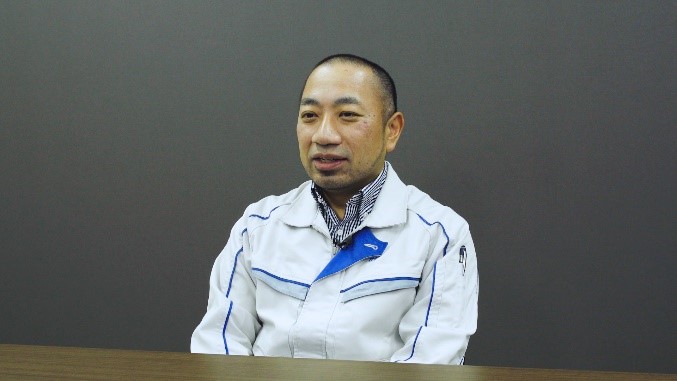
MotionBoardとi-Reporterで、製造工程の管理帳票と測色傾向分析をデジタル化
そこで同社は、帳票デジタル化ツールとしてシムトップス社の「i-Reporter」 、データ可視化ツールとして「MotionBoard」を導入した。
管理帳票業務では、i-Reporterのタブレット入力やBluetoothによる測定器との連携機能により、入力業務を大幅に効率化。MotionBoardと連携することにより、管理グラフ図の自動描画と共に、異常傾向のアラート表示までの自動化に成功した。
塗装工程では、センサーから入力された測色管理データベースとMotionBoardを連携。車種、塗色ごとの傾向グラフを自動表示させ、しきい値を超える前の対応が可能となり、不具合の未然防止につながっている。
菅原氏はその成果を、次のように評価する。「何千帳票、それも毎日多くの作業員が行っていた手書き起票やグラフ描画を自動化できた業務改善効果は計り知れません。また、測色管理においても確実性が増すことに加えて、不良の兆候を捉え、設備を調整することで未然に防止できる。結果として製品のバラツキの発生を抑制できていると感じています。」
MotionBoardを採用した決め手とは?
情報システム部 DX推進室 生産DXグループ グループ長の後藤 佑介氏は、MotionBoardの選定経緯と採用の決め手について、次のように話す。「他社の工場を見学した際、見事に可視化された画面を見ました。現場の方々から『MotionBoardで、自分たちでやりました!』と聞いて、凄いなと思ったのが最初の印象です。データの可視化について、当初は自社開発を検討していましたが、クラウドサービスなら工数をかけることなく、スモールスタートできます。他のクラウドサービスとも比較しましたが、どれも当社の要件にフィットせず、操作しにくいなど、決め手に欠けました。MotionBoardは、Excelでできることは一通りできることに加えて、基準値を超えたら異常をアラート通知する、動的にスケールを変えられるなど、可視化のための機能が優れており、当社の要件にも柔軟に対応できると感じました。さらに、製造現場の作業者でも使える操作性の高さが、採用の決め手となりました。i-ReporterとMotionBoardの連携は、当初から意図したものではなかったのですが、相互の連携性が高く、さらに効果が高まりました。MotionBoardはExcel、CSVから基幹システムや他の管理ツールまで、さまざまなデータベースと連携しやすい点も魅力です」
同社は当初、MotionBoard Cloudを利用していたが、成果が得られたことで全社への展開を決断。オンプレミス版のMotionBoardに移行した。この理由を後藤氏は、「クラウド版はユーザー課金なので、全社員で利用するならオンプレミス版の方が、コストメリットが高かったためです。自社の状況やニーズに合わせて導入方法が選べるのも、MotionBoardのメリットだと感じます」と話す。
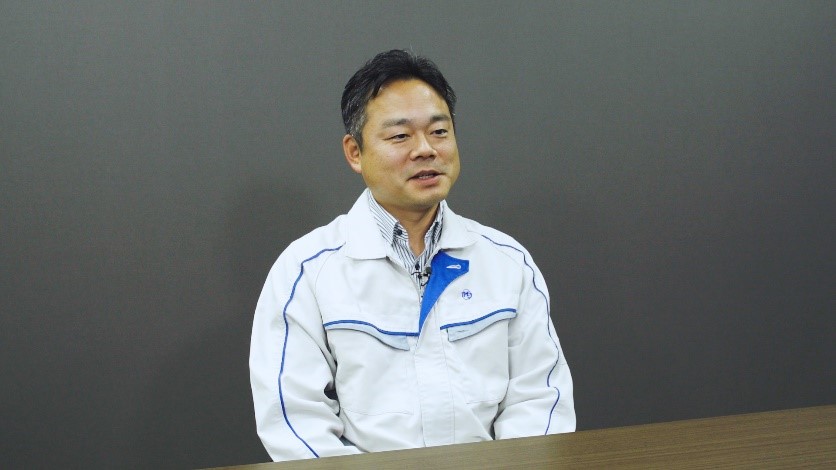
その他の製造現場での活用からリアルタイムな生産状況の把握
全社展開後の製造工程におけるもっとも大きな効果は、「生産管理板」と呼ばれる、生産計画と実績との管理とのこと。同社では1時間=1ラウンドとして、何か不具合が発生すればそのラウンドごとに手を打つ改善活動を実施している。従来は、そのデータ取得から掲示までを手作業で行っていたが、現在は基幹システムや生産設備からデータ連携し、MotionBoardで自動描画。紙による一覧掲示から現場に配置した大型モニターへの投影へと変えたことで、管理者が必要なデータをすぐに確認することができ、掲示場所への移動時間の削減と共に、タイムリーな状況把握を実現した。
菅原氏はその効果をこう話す。「各ラウンド中における上司の呼び出し回数や、停止時間の多い工程を自動で表示することで、管理者は工程内の状況が把握しやすくなり、可動率の向上につながっています」
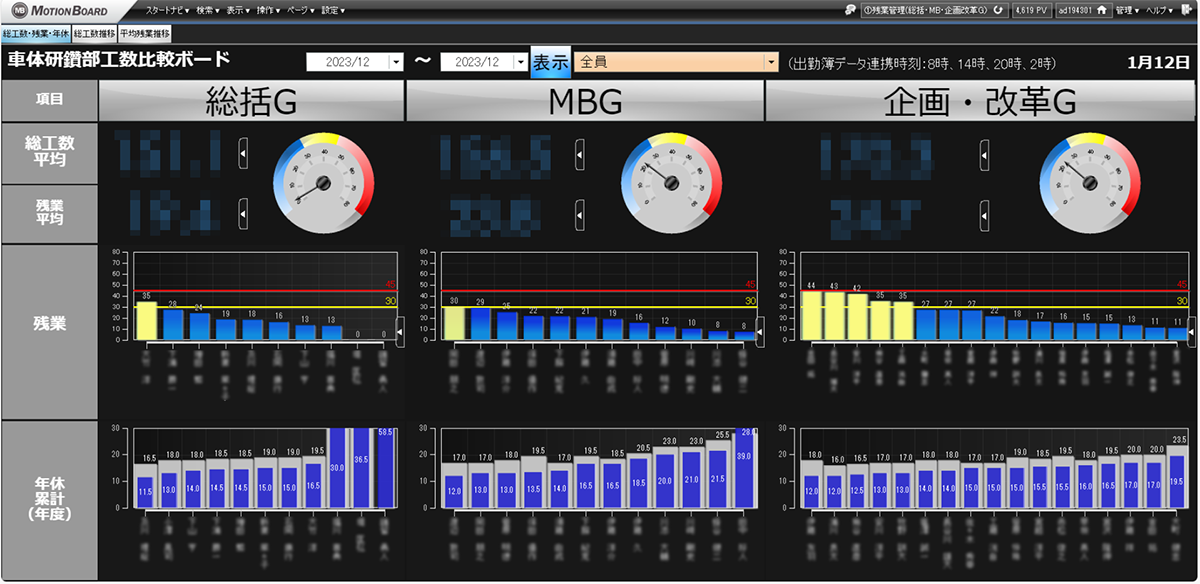
勤怠管理などの管理業務にも拡張、Excelによる管理負担を軽減
また、同社は製造現場のみならず、MotionBoardをさまざまな管理業務にも活用している。
情報システム部 ITマネジメントグループ 主任の滝本 仁氏は、その成果を次のように話す。「出勤簿システムのデータをMotionBoardと連携させて、残業や年休取得率の見える化を行っています。それも、みんなに見えるように大型のディスプレイに表示させています。計画通りでないと赤く光るので、牽制効果が高いです。他にも各部の経理管理やプリンターの印刷枚数の見える化などを行い、管理業務の効率化やペーパーレス化にも役立てています」
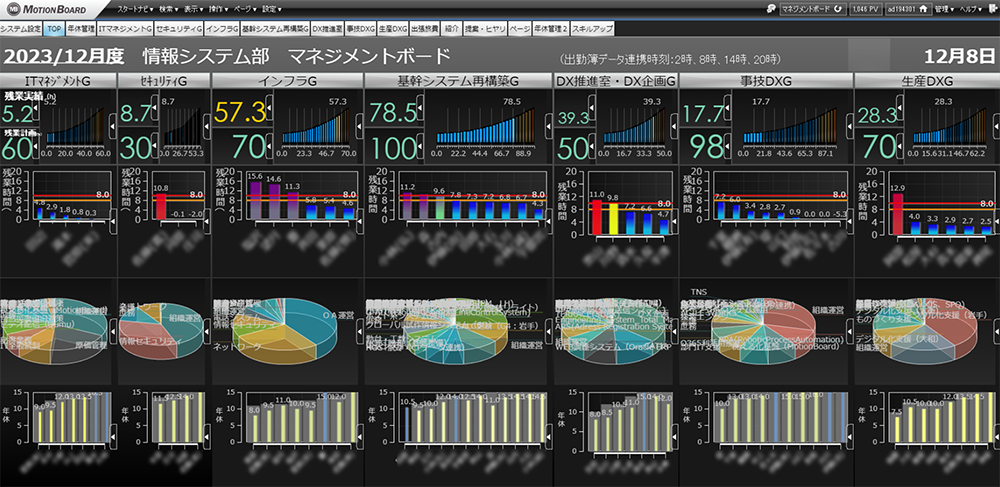
さらに滝本氏は、コロナ禍での職域接種の管理システム開発にもMotionBoardを活用。「突然、職域接種での状況を管理するシステム開発の必要性に迫られたのですが、MotionBoardを活用することで、スピーディに対応できました」と、その成果を語る。
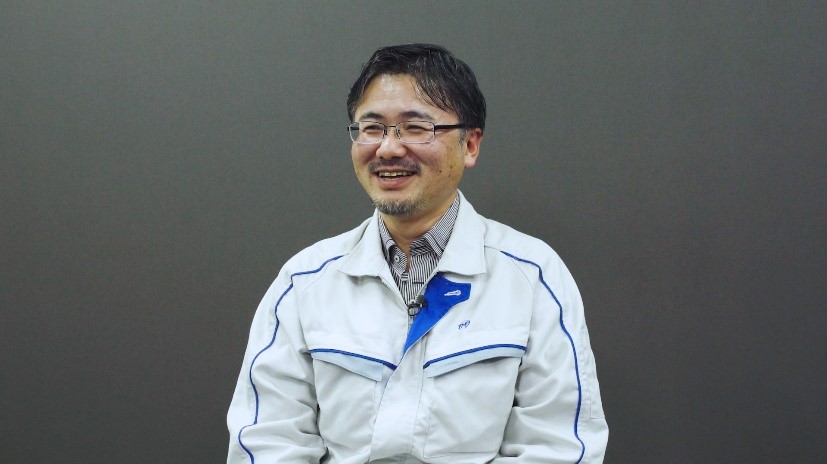
着実に社内にデータ活用が浸透、さらなる使いこなしでDXを加速したい
こうして社内データの見える化ツールとして浸透したMotionBoard。導入当初5名ほどだった利用者は、現在700名超まで拡大。定期的な勉強会の開催、使い方教育動画を作成するなど、普及が進んでいる。
その活用効果について、菅原氏は次のように話す。「当社はもともと色々な情報を多くの人に分かるよう掲示したり、異常をいち早く検知するためにランプが光るアンドンなど、改善活動に意欲的な文化があります。ただ、それらをデジタル化しようとしたとき、Excelでは限界がありました。MotionBoardは見える化の考え方がベースとしてあるので、やりたいことが標準の機能でほとんど実現できます。従来の手書きの紙を掲示するやり方から、データを自動で収集、グラフに描画し、異常があればスピーディに誰もがわかるよう、大型ディスプレイに映すようになってきた。改善活動に置いて、異常のポイントをわかりやすく行灯(あんどん)のように示してくれるのが、当社にとってのMotionBoardを活用する価値だと感じています」
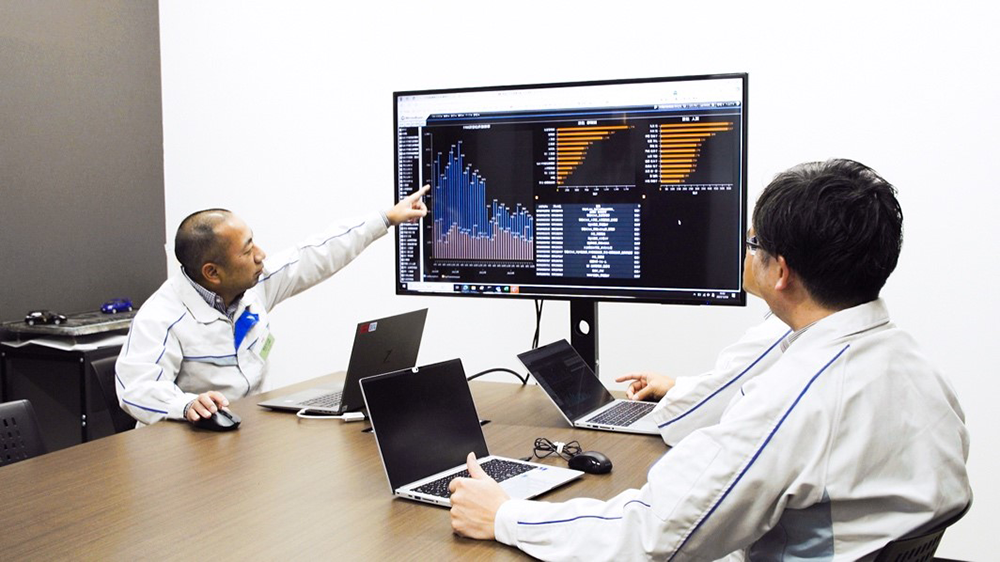
滝本氏は、これまでのウイングアークの支援について、次のように評価する。「問い合わせすると、常にしっかり対応いただけています。分かりやすく設定情報も提供され、細かな点はサポートしていただける。国産メーカーならではのきめ細やかさで、安心して活用できます」
同社ではこれまで、情報システム部内に人材を集めたDX推進室を設置し、デジタル人材の育成に取り組んできた。今後は、そこで育った人材が各現場に入り込み、さらなるDXの推進加速を目指しているという。最後に菅原氏は、今後について次のように結んだ。「デジタル化は手段であって、目的ではありません。デジタル化して何を目指すのか、何を目的にしているのかを常に意識して進めていくことでDXの実現につながると思います。その時に、MotionBoardはすべてのデータの合流地点になるイメージです。この数年間で社内にかなり浸透して、データを見る人は確実に増えました。どう使うか、という議論ができるようになったことが一つの成長とも感じます。これからは、一人ひとりがもっと自分でアイデアを出して、使いこなせるようにしていきたいと思っています」
Company Profile
トヨタ自動車東日本株式会社
設立:2012年
所在地:宮城県黒川郡大衡村
事業内容:トヨタグループの中核を担う開発・生産拠点として乗用車を中心としたトヨタ車の企画開発、生産を行っている
URL: https://www.toyota-ej.co.jp
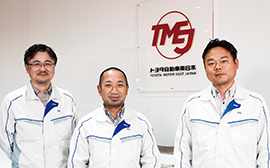
左から
情報システム部 ITマネジメントグループ 主任 滝本 仁氏
インフラグループ グループ長 菅原 吉規氏
DX推進室 生産DXグループ グループ長 後藤 佑介氏
導入製品
MotionBoard
BIツールを超えたダッシュボード「MotionBoard」。様々なデータをリアルタイムに可視化。クラウドサービスは月額30,000円から