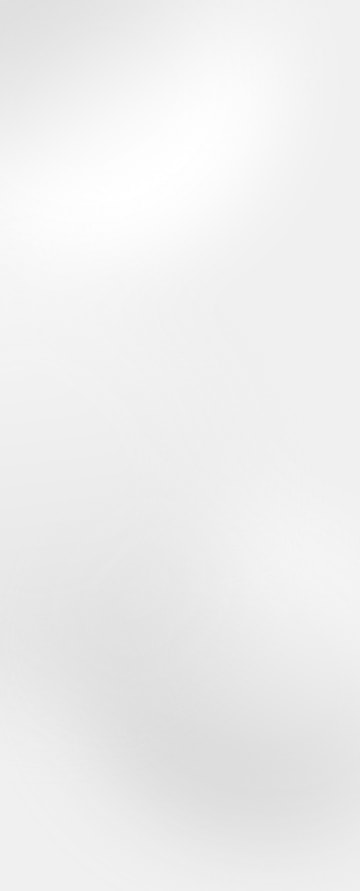
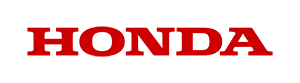
本田技研工業株式会社 鈴鹿製作所
現場主導・ボトムアップでDXを推進
データ活用を現場に定着させる創意工夫で得た着実な成果
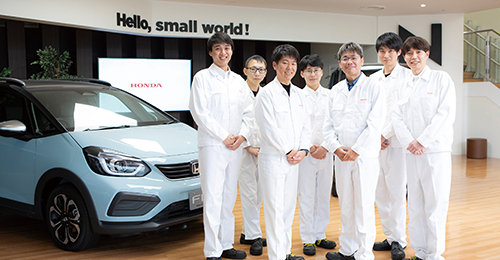
- 製品
本田技研工業株式会社 鈴鹿製作所(以下、鈴鹿製作所)は、2017年の新ライン立ち上げ計画を期に、MotionBoardの導入を検討。現場主導、ボトムアップでのDX推進を目指した同所は、業務アプリ開発などの工夫で現場への定着を図り、製造ラインやワーク状況の見える化、トレーサビリティ検索、変化点の時間軸傾向など、多様な画面を開発。その結果、現場にデータ活用の文化が根付き、部門連携、若手の登用やデジタル人材育成など、大きな成果を上げ続けている。
導入背景
●2017年に新ライン立ち上げプロジェクトが発足、社外、社内でもDX推進気運が高まる
●2019年に新ライン立ち上げ完了、MotionBoardによるデータ活用の取り組みを開始
●人手不足や脱炭素などの社会課題も見据えて、データセントリックな働き方への移行を目指す
- 課題
-
- これまでさまざまなツールを導入したが定着せず、現場に必要性への理解が得られなかった
- 日々使う現場がイニシアチブを握って自ら作り、ノウハウを残していかないと、継続的な運用も進化もできない
- 解決策導入ポイント
-
- 食堂メニューや備品発注などの身近な業務アプリをダッシュボードで開発、現場の人たちにデータ活用の体験を促す
- 製造ラインおよびワーク状況の見える化、トレーサビリティ検索、変化点の時間軸傾向など多様な画面を開発
- 生産現場を止めない、現場でも入力しやすいといった工夫を施した
- 効果
-
- 利用部門だけの成果として、紙帳票約800枚、関連工数800時間/月の削減に成功
- 不具合/不良発生率/PDCA高速化/稼働達成率/エネルギーコスト削減などの数値目標をいずれも達成
- 現場にデータ活用の文化が根付き、部門連携、若手の登用やデジタル人材育成などの効果も得られた
現場主導・ボトムアップでDXを推進した理由
1960年、Hondaの国内3番目の工場として設立された鈴鹿製作所。世界ベストセラーカーのフィットをはじめ、軽自動車のNシリーズやハイブリッドカーを生産するほか、海外28ヶ国のHonda工場に部品を供給、現地生産活動を支える重要な役割を果たしている。同所では2017年、シリンダーヘッド・ブロック加工ラインの新ライン立ち上げプロジェクトが発足。まだDX(デジタルトランスフォーメーション)が定着する以前から、IoTやICTの活用を模索していた。そして2019年、新ラインが無事に完成。その中で、MotionBoardを活用した見える化を進めてきた。
鈴鹿製作所 エンジン工場 エンジン機械モジュール アシスタントチーフエンジニアの池口 大輔氏は、当時の状況を次のように話す。「その頃、経済産業省から『DXレポート』が発表されて、“近い将来、嫌でも仕事のやり方が変わる”と感じていました。これまでの人が主役で人が判断、分析するやり方では、少子高齢化による人手不足や、脱炭素などさまざまな社会問題にも対応できなくなる。当社でもその後2021年に、社内に向けた『Honda DX宣言』も表明されました。こうした流れの中で、鈴鹿製作所では活動スローガンに『まずやるDX』を掲げ、脱炭素やGX(グリーントランスフォーメーション)も見据えた、本格的なデータ活用の取り組みを推進しました」
本社側やIT部門に体制を作る企業が多い中、鈴鹿製作所ではDXをボトムアップで推進している。それも製作所全体の横串でもなく、エンジン工場内のユニットメンバーでDXを推進した点がユニークだ。「ITなど他部門が作るシステムでは、どうしても現場が実現したいこととデータの持ち方や作り的なところで、乖離が生まれます。それを埋めるには、今後使っていく現場が自らイニシアチブを握り、ノウハウを残していかないと、この先運用も進化もできないと考えました。ですので、IT部門には監査的なところをお願いして、基本的に全て現場、工場の1部門で全てをやり遂げる形で、推進体制を組んで進めました。」(池口氏)
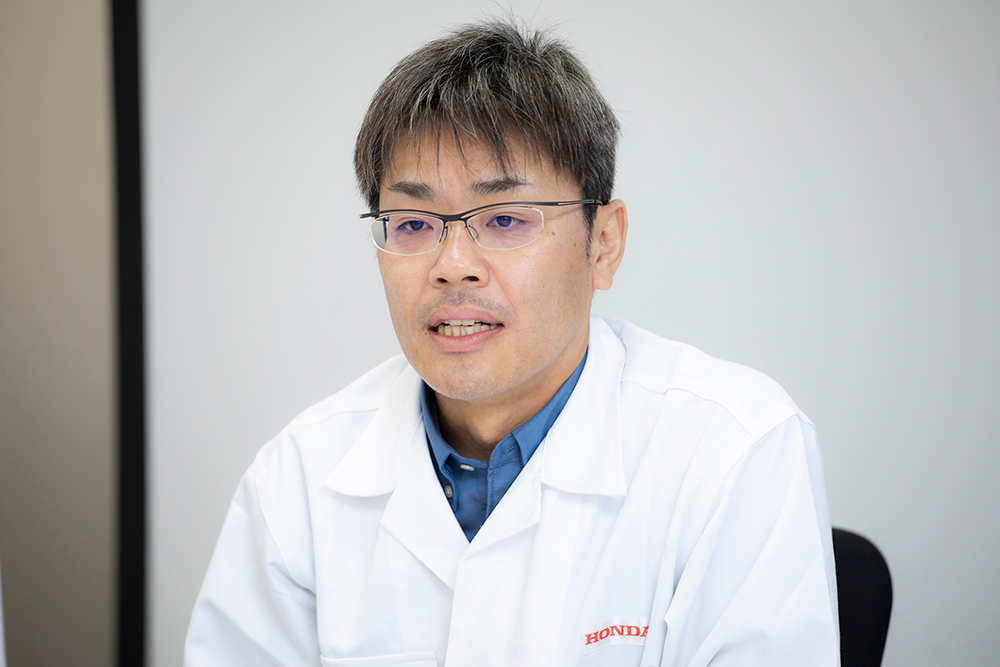
MotionBoardを選んだ6つの理由
鈴鹿製作所が数あるBIツールの中からMotionBoardを選んだ理由は、大きく6点ある。「リアルタイムで表示できる」「自分たちで作り込める」「データ入力できる」「オンプレミスで導入できる」「製造業にマッチしている」そして、「帳票ベースで出力できる」ことだ。
特に重要視したのはリアルタイム表示。「いま何が起きているのか?が、製造現場ではとにかく重要。営業ツールのように1日後や1週間後では遅過ぎて、現場ニーズにコミットできません。品質データに変化が起きていることに現場が即時にアクションを起こせないと、PDCAが遅くなります。」(池口氏)
また、「自分たちで作り込める」については、「プログラミングもデータベースも詳しくない我々でも作れるためにノーコード開発から始められて、その後に凝った作りもできる開発の自由度の高さ。近所に同じ製造業でMotionBoardを活用されている富士フイルムマニュファクチャリング社の事業場があり、実例およびノウハウを共有いただけたこと、ウイングアーク1stのメーカーサポートが充実していることも、安心感がありました。」(池口氏)
そしてMotionBoardは、データ入力・収集から帳票出力まで1ツールで完結する。「現場からも入力しやすい手法で取得したデータは、日報や帳票などとの紐付けが重要です。これはいくつかのツールを使えば可能ですが、できるだけシンプルにしたかった。それがリアルタイム性にもつながります。手書き帳票は読みづらく、どうしても属人的になる。MotionBoardならそれも防ぎ、業務を標準化できる。さらに現場の方がなじみのあるフォーマットで帳票出力できるオプション機能も備わっている点が、魅力でした。」(池口氏)
「生産現場を止めない」工夫と、実際の活用イメージ
MotionBoardの導入にあたっては、「上位でサーバーが止まっても、生産を止めない」、製造業ならではのコンセプトに基づいている。PLCやデータベースなどさまざまなサーバーに蓄積されたデータは、1次処理して言語化。CSV化したデータをETLで2次処理、モデル化して、MotionBoardでビジュアル化する流れとなっている。
同所はさまざまなシーンでMotionBoardを活用しているが、ここでは代表的な活用イメージを、画面と共にご紹介する。
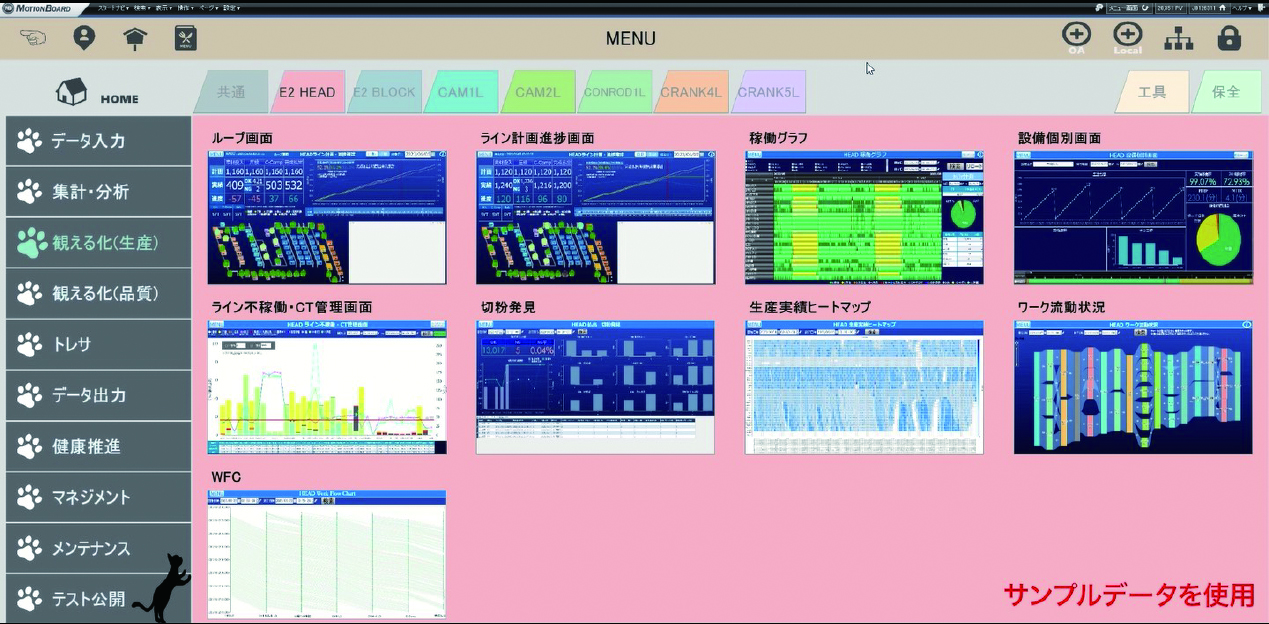
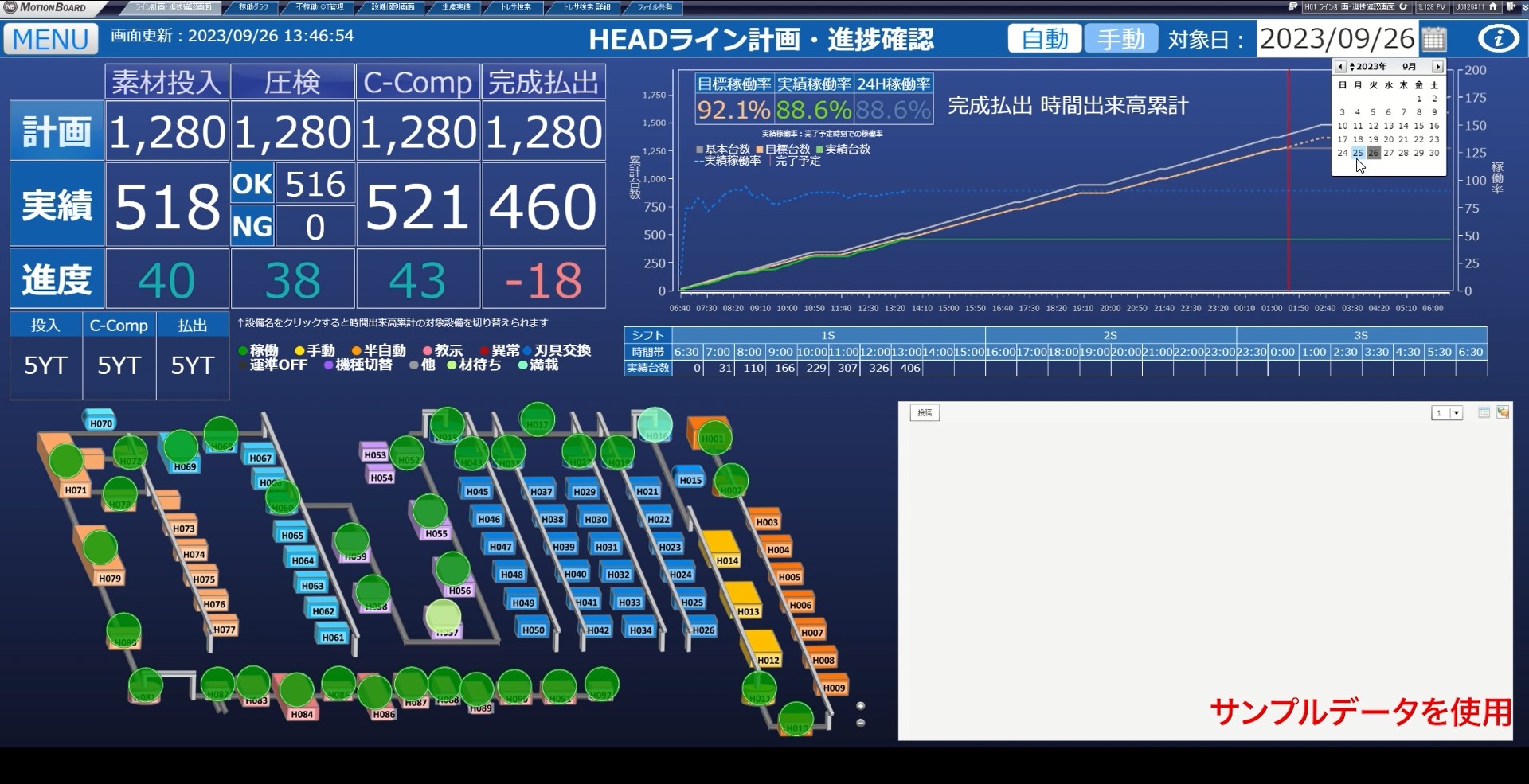
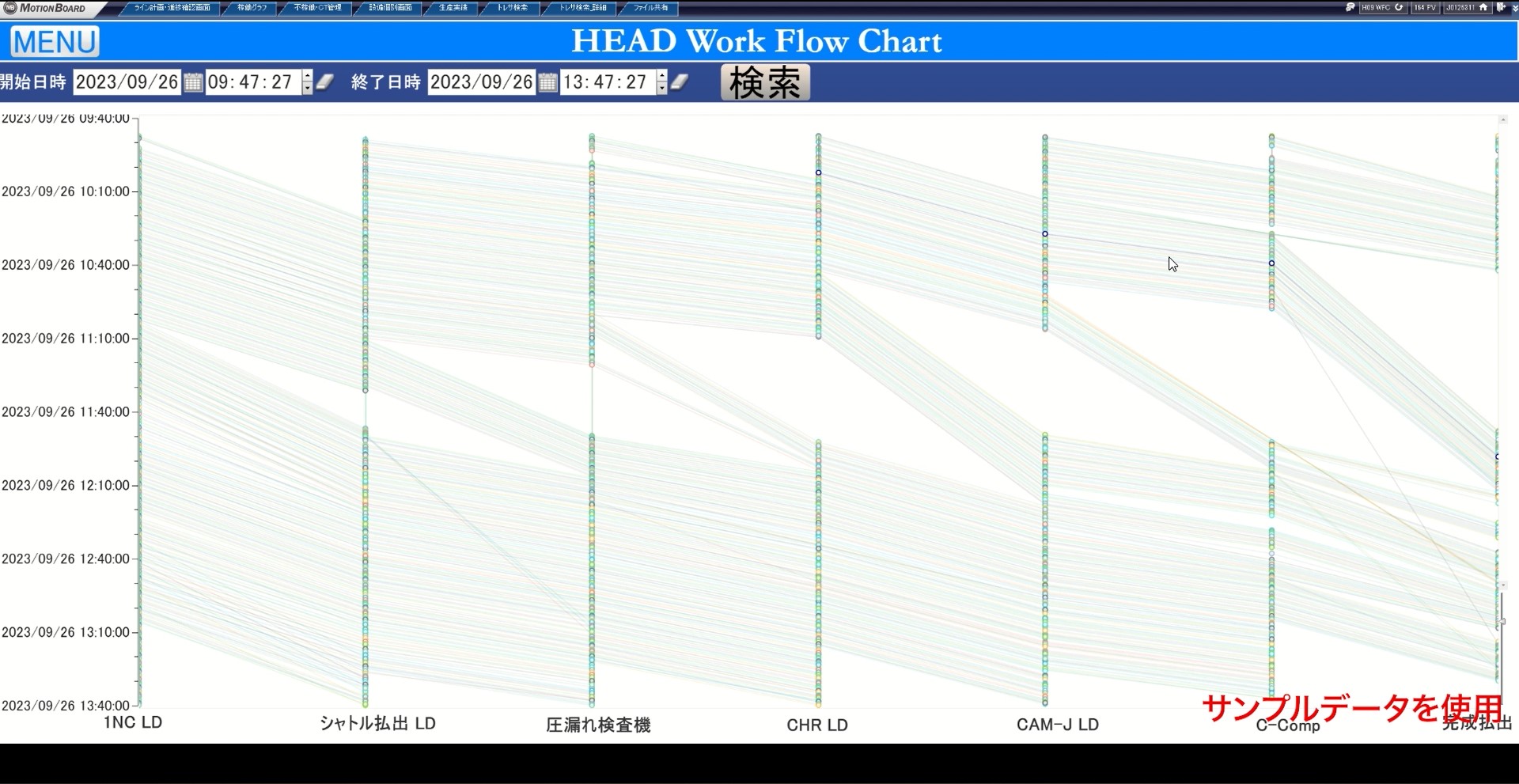
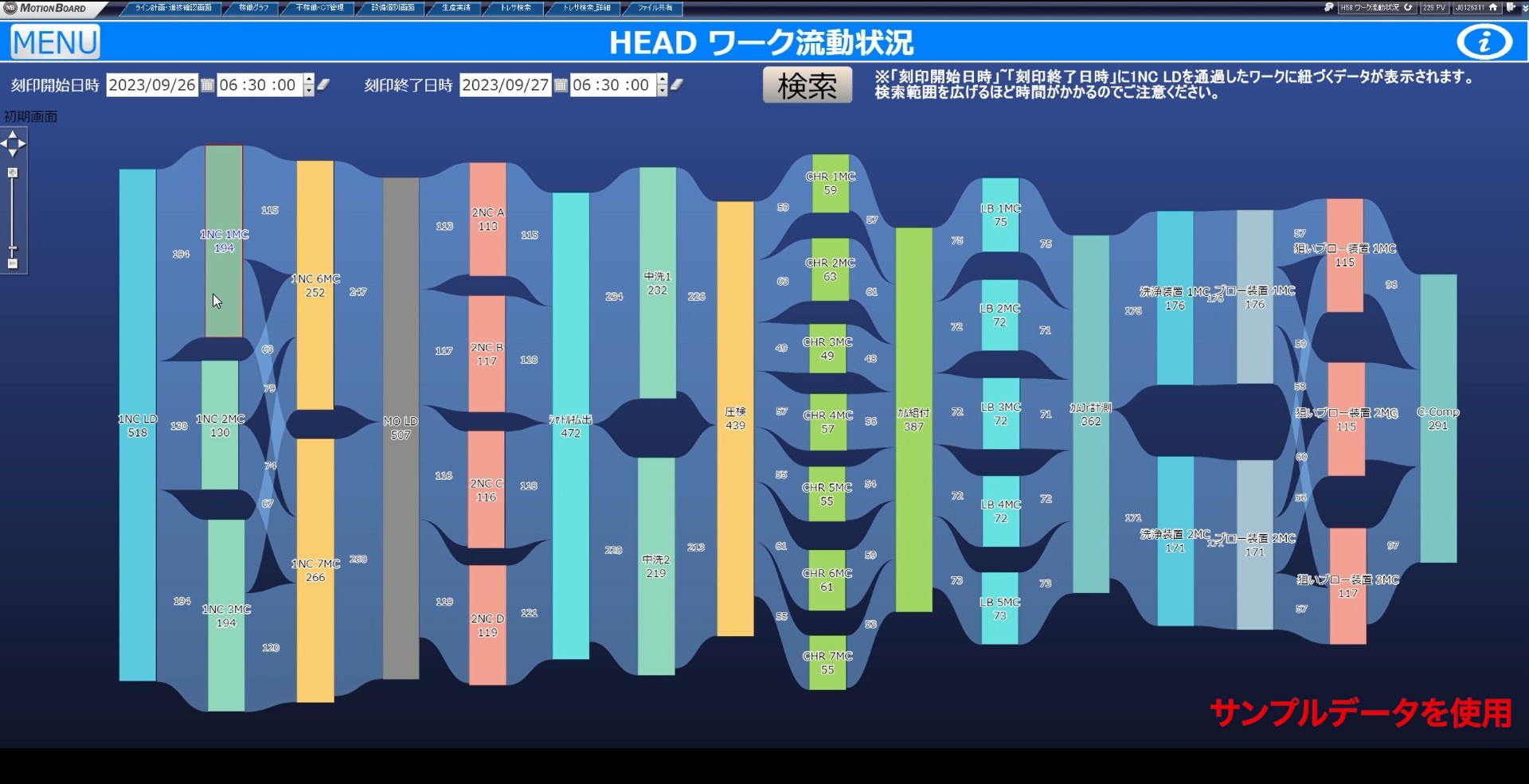
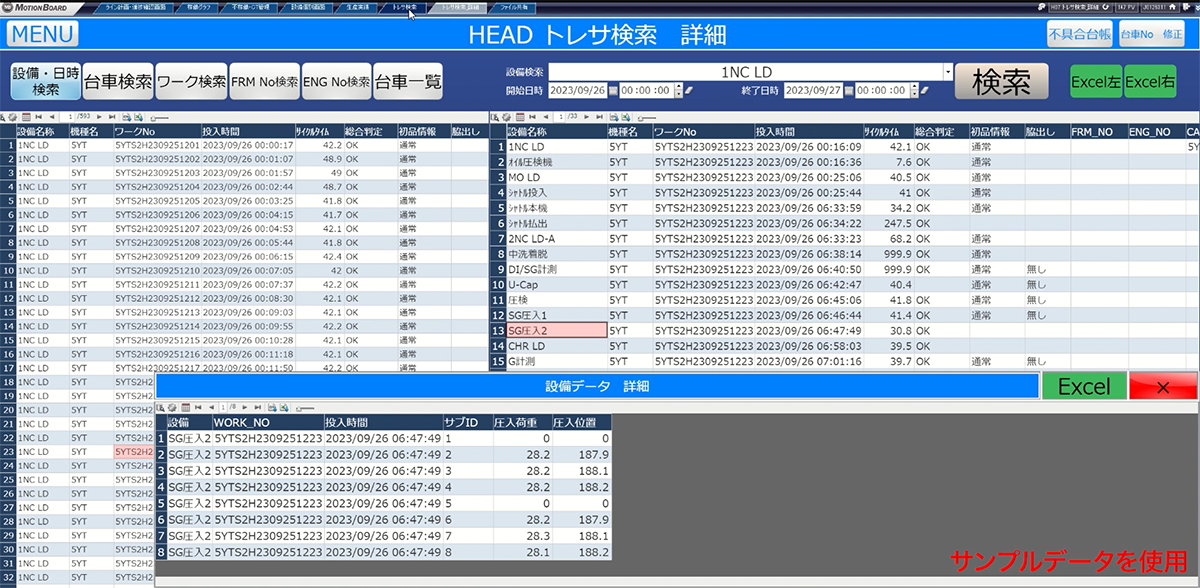
トレーサビリティの画面では製品や部品の固有番号で検索すると、どのような経緯で物が流れてきたのか、成否データなどが一つ一つ紐づいて表示される。何か不具合が起きたとき、その前後にどこで何が流れていたのか?などが瞬時に見つけられることで、影響範囲も特定しやすい。特にここは表示スピードにこだわり、大きな工数削減と業務の属人化防止につながっている。
浸透までの壁を乗り越えた、「まずはログインしてもらう」ための工夫
このように積極的な画面開発を続けた鈴鹿製作所。しかし当初、現場利用はなかなか進まなかったという。「実は当所ではこれまでも何度か、同様のシステムを開発したもののことごとく失敗、わずか数年で使えなくなってしまい、現場には嫌なイメージしかなかったのです。そのため、今回のMotionBoard導入当初も現場はものすごく否定的で、ログインすらしてもらえない状況が続きました。」(池口氏)
推進チームはこの状況を打破すべく、さまざまな工夫を施す。1つ目は、MotionBoardを活用した食堂メニュー画面の開発。開発を担当したアシスタントチーフエンジニアの青木 雅弥氏は、その理由を「現場の作業員の楽しみといえば食事です。とにかくまずはMotionBoardを触ってもらい、難しいものじゃないんだよ、と伝えたかった。」と話す。
2つ目は、文房具や備品の発注を一元化した画面。「これまでは、紙の一覧表を見てラインごとの注文書を手書きしていました。一覧表だとどんな品物か分かりづらい、注文したのに在庫切れ、誰がいつ発注したのか分からないなど、さまざまな困りごとがありました。そこで裏側で在庫管理と連動した画面を作ることで、発注側にも管理する人たちにも体験してもらい、貢献することで、MotionBoardはこんな業務アプリのような使い方もできるんだ、と理解してもらいました。」(青木氏)
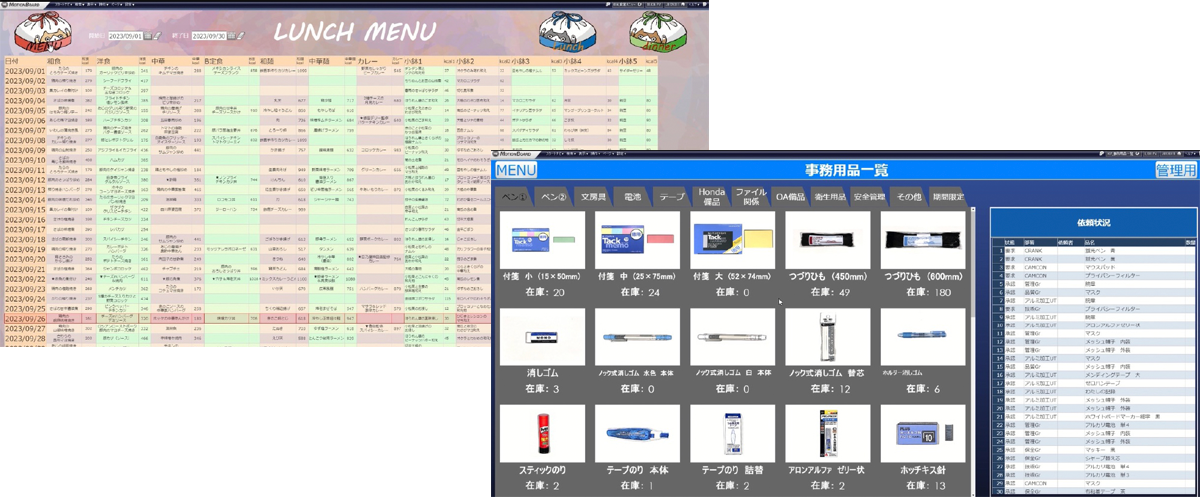
これらMotionBoardによる日常業務に溶け込んだダッシュボードの開発は、大きな効力を発揮。しだいにMotionBoardにアクセスする人が増え、所内でのデータ活用の裾野は、着実に広がっていったという。
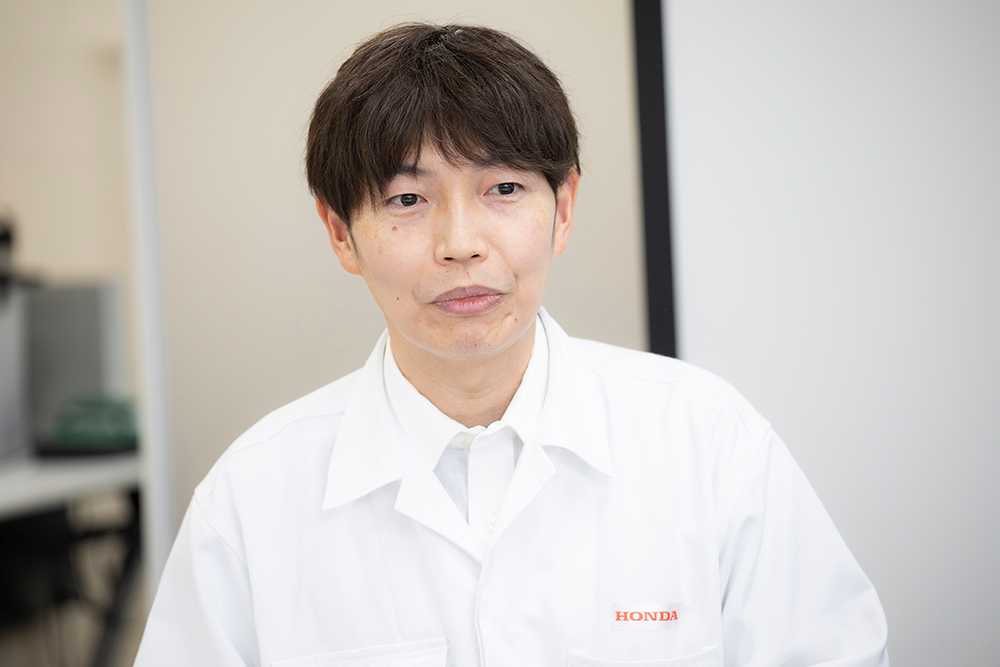
変化点を時間軸で可視化・入力への工夫
こうして、所内のデータ活用ツールとして浸透したMotionBoard。ここで、品質の維持が求められる製造業ならではの特長的な活用方法と、課題となりがちな入力の工夫について紹介する。
同所では、刃物交換などについて、紙の日報を直接MotionBoardに入力してもらい、生産設備の生のデータと掛け合わせることで、変化点の傾向を可視化している。
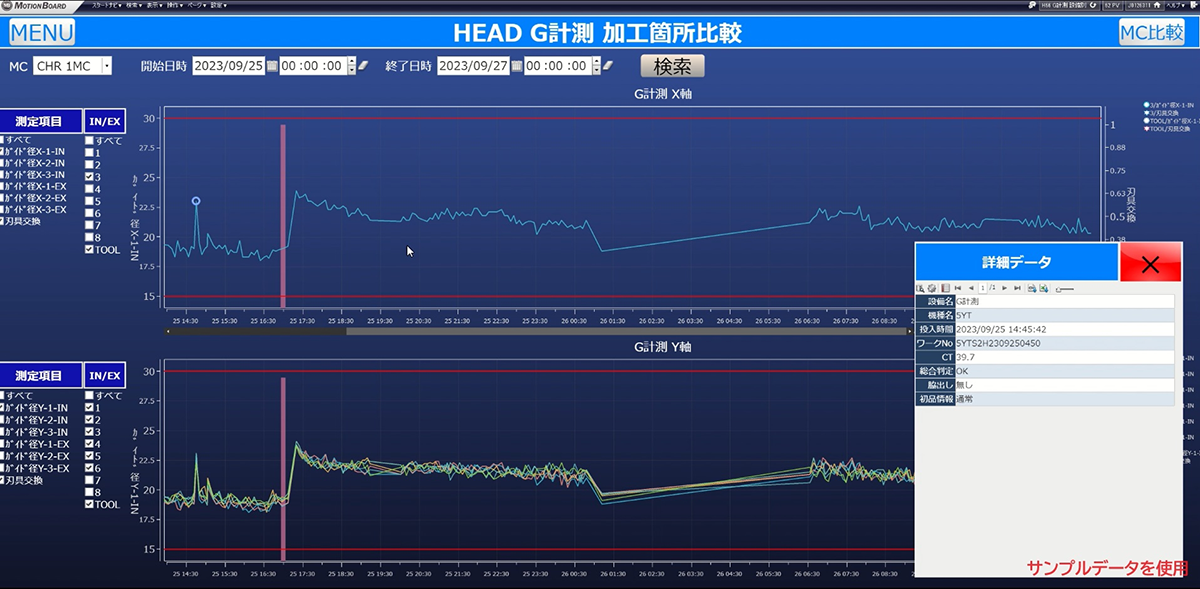
これにより、現場はどのタイミングでどのような変化が起きたのか、その傾向が一目で掴みやすい。「こうした変化はこれまで、人が紙の日報と突き合わせて調べ、ラインごとのCAP(点検/改善/計画)会議で、ホワイトボードに手書きで共有していました。それをリアルタイムに見える化したことで、属人的な経験値や勘に頼ることなく、改善のスピードアップと共に、工数削減も体感できるようになりました」(青木氏)
また、同所はカレンダーやステッパーなどを独自でカスタマイズ。手袋をした作業員がキーボードを使う必要もなく、大型ディスプレイやタブレットのタッチ操作で入力できるUIを開発した。
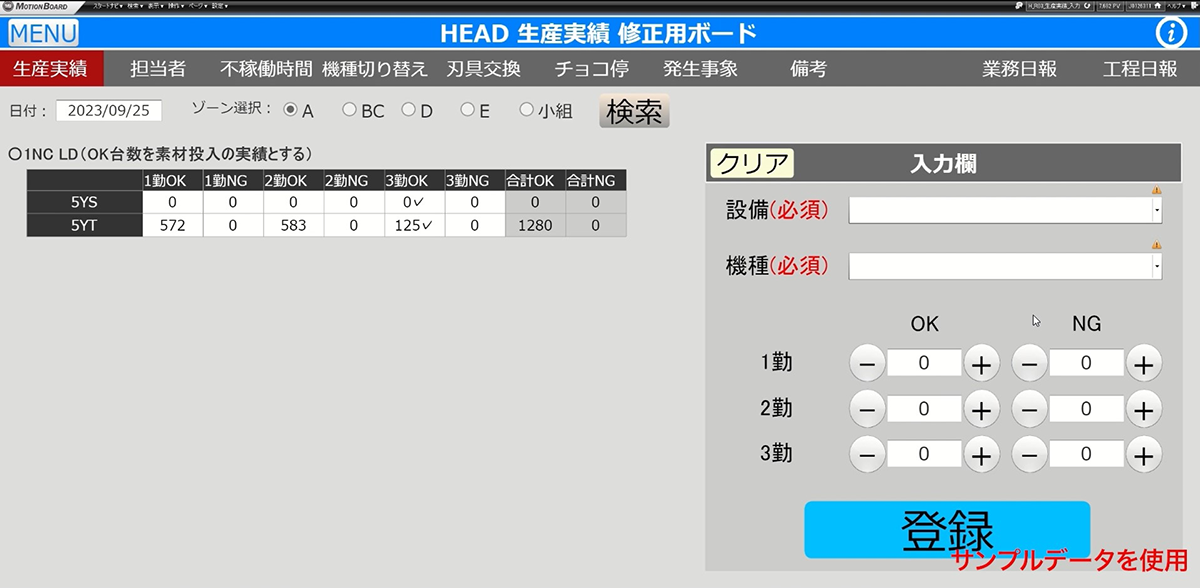
さらにIDと連携させて入力者の選択を省力化するといった工夫も施している。「これにより現場には紙やペンがなくなり、ディスプレイとタブレットで業務が完結できるようになりました」(中田氏)
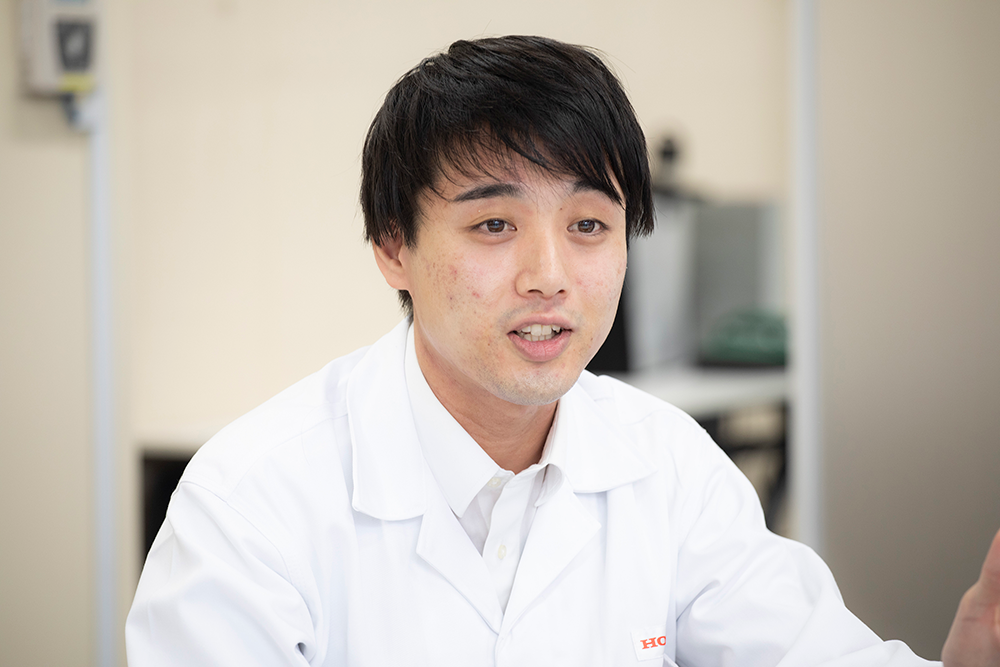
帳票800枚、工数800時間/月削減、各種目標数値達成など大きな成果
こうした取り組みの成果は、確実に数値となって表れている。MotionBoardを活用する一部部門だけの実績として、削減した紙帳票は月に約800枚。その帳票をデータに転記、分析といった工数はおよそ800時間/月削減された。
そしてその結果、不具合や不良の発生率、PDCAの高速化、稼働達成率、エネルギーコスト削減など品質、生産、環境分野における目標数値もすべて達成し、その効果は年々、高まっているという。「これまでの属人的な業務が見える化、標準化されて、業務の引継ぎもしやすい。そして、生産効率だけでなく、品質向上にも貢献しています」(青木氏)
さらに池口氏は、現場の雰囲気の変化について、こう述べる。「エンジン工場としてデータ活用を現場に浸透させ、定着させた結果、現場からは楽になった、便利になった、データ活用を一緒にやりたいから教えてください、といった声が挙がっています。まさしくこれが、我々のやりたかったこと。製造現場DXを浸透できたことが、MotionBoardを導入した最大の実績だと感じています」
データ活用の成果を他の部門へも展開、デジタル人材の育成にも取り組む
今後について、生産業務部 事業管理課 アシスタント チーフエンジニアの中尾 祐氏は、「これらの実績と成果を、他のラインや事業部へも広く展開したいと考えています。MotionBoardは、互いの課題を持ち寄って共に解決策を話し合うきっかけになるなど、部門間連携のコミュニケーションツールとしても有効です」と語る。
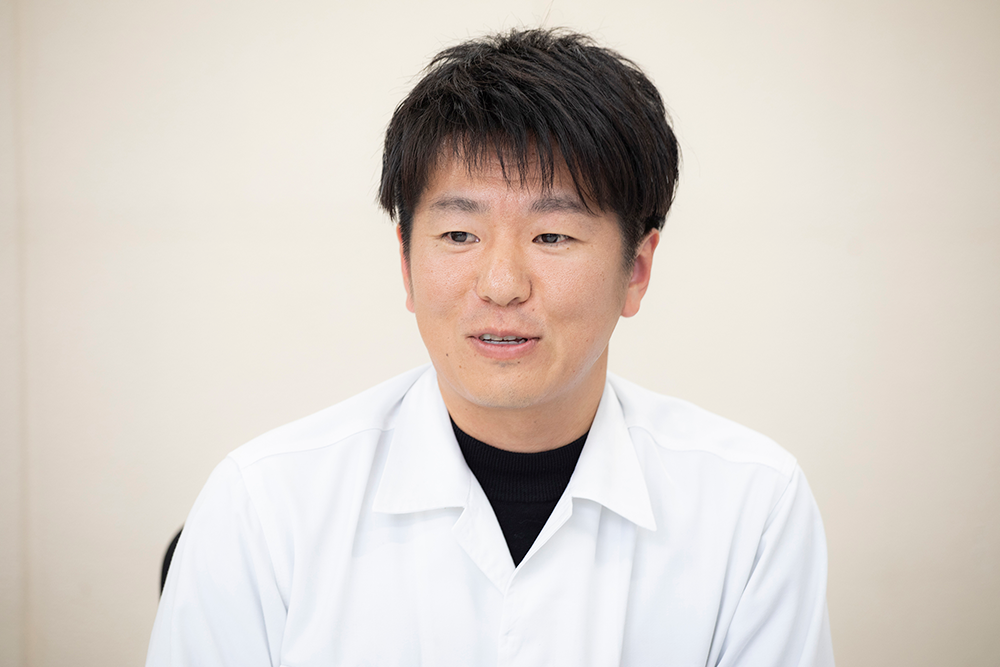
そしてMotionBoardは、若手の登用やデジタル人材の育成にも貢献しているという。「データ活用の画面開発では、入社1~3年の若手社員が活躍しています。現場の課題を知り、解決策を考える中で、業務の本質を学ぶ機会にもなる。デジタルスキルマップを作成するなどして、そうした人材育成にも取り組みたい」(青木氏)
最後に池口氏は、これからの活用とウイングアーク1stへの期待を、次のように結んだ。「この数年間、さまざまなデータの取得・分析が進みました。これからは、見えるだけではなく、AIを連携させ知能化して、さらなる進化に取り組みたい。これからもウイングアーク1stには、現場の改善に有用なソリューションやサポートの提供に、期待しています」(池口氏)
Company Profile
本田技研工業株式会社 鈴鹿製作所
設立:1960年
所在地:三重県鈴鹿市平田町1907
URL:https://global.honda/jp/suzuka/
Hondaの国内3番目の工場として設立。世界のベストセラーカーのフィットをはじめ、軽自動車のNシリーズやハイブリッドカーを生産している
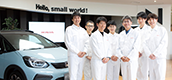
本田技研工業株式会社
四輪事業本部 生産統括部 鈴鹿製作所
エンジン工場 エンジン機械モジュール
アシスタントチーフエンジニア
池口 大輔 氏(前列右から2番目)
エンジン工場 エンジン機械モジュール
アシスタントチーフエンジニア
青木 雅弥 氏(前列1番右側)
エンジン工場 エンジン機械モジュール
中田 昇太郎 氏(前列1番左側)
生産業務部 事業管理課
アシスタント チーフエンジニア
中尾 祐 氏(前列右から3番目)
導入製品
MotionBoard
BIツールを超えたダッシュボード「MotionBoard」。様々なデータをリアルタイムに可視化。クラウドサービスは月額30,000円から