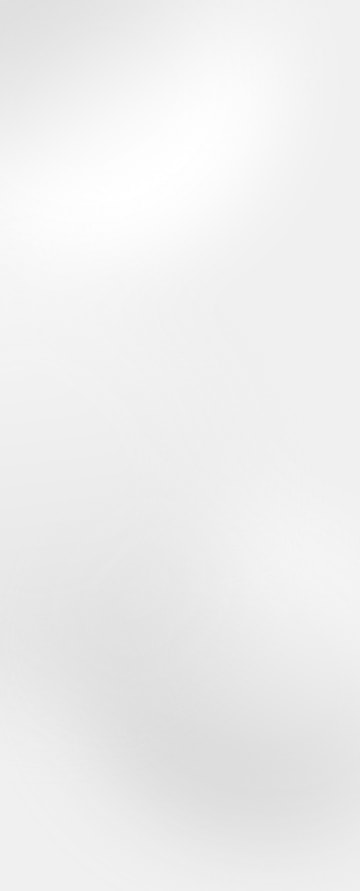
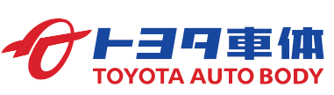
トヨタ車体株式会社
データ分析で慢性的不具合を解消
「現場による、現場のためのDX」
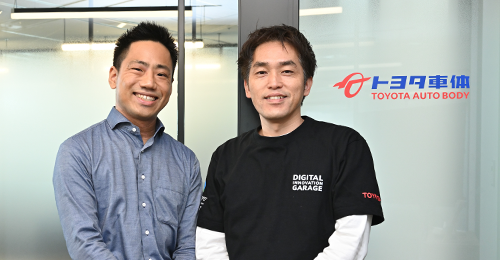
- 業種
-
製造
日本のものづくりを語る上で欠かせないTPS(トヨタ生産方式)。最前線で体現してきたトヨタ車体は、TPSとデジタルを融合しカイゼンの進化に取り組む。トヨタ車体 吉原工場の塗装部で取り組んだ「データ活用による慢性的不具合の解消」は成功モデルの1つ。現場に馴染みやすいウイングアークのBIツール「MotionBoard」を活用した。吉原工場 塗装部は、ウイングアークの伴走型サポートを受け、特定した不具合の不良率40%削減を実現。成果が出たことで、さまざまな慢性的不具合の要因特定に取り組みを広げている。
導入背景
2016年に完成車両メーカーに移行したトヨタ車体では、デジタルを活用した現場の体験価値向上、業務改善活動に着手。デジタル活動方針の3本柱に従って、現場主導によるボトムアップでDXを進めている。その足がかりとしてMotionBoardを導入し、「慢性的不具合をなくす」取り組みにチャレンジした。
- 課題
-
- 事業移管に伴い、DXのスピーディな推進、技術やスキルを生かした「コトづくり」などを今後のあるべき姿に設定
- 慢性的な不具合が発生していたが、要因がつかめずにいた
- 解決策導入ポイント
-
- 暗黙知のデータ化、見える化、データ分析・解析、最適化の4プロセスでデジタル化を促進
- ウイングアークと電通総研よりDX診断サービスを受け、吉原工場 塗装部における慢性的不具合の要因特定・改善をスタート
- 現場で使う観点から、ワンパッケージ型、伴走型サポートの条件を満たすMotionBoardを採用した
- 効果
-
- MotionBoardの分析機能により、項目を切り替えるだけでスピーディに分析の考察が可能に
- 従来に比べて精度の高い管理値(閾値)を導き出し、その管理値を運用ラインに適用することで該当不良に関して不良率40%削減(従来比)を実現
- 今後はAIによるサポートでさらなる省力化を図るとともに、人材育成の強化、データ活用の定着など、現場の変革にも力を入れていく
現場主導のDXを成功に導くカイゼンの進化とは
1945年、トヨタ自動車工業(現:トヨタ自動車)の刈谷工場が独立しトヨタ車体が誕生した。大きな転換期となったのは2016年。トヨタ自動車のカンパニー制を機に、トヨタ車体は商用車、ミニバン、SUVの完成車両メーカーの道を歩み始めた。
トヨタ車体 デジタル変革推進部 主査 兼 商用営業部 主査 寺倉 隆治氏は振り返り、こう話す。「従来は、トヨタ自動車から商用車の開発・生産を委託されていました。事業移管に伴い、当社で商用事業を担うことになりました。当時、生産技術部に在籍していた私を含め有志4人で、今後の会社について話し合う中で、DXのスピーディな推進、当社の技術やスキルを生かした『コトづくり』など、やるべきテーマを導き出しました。それらを実現するべく、まずは自分たちが主体的に取り組むことができる現場から、デジタルを活用した現場の体験価値向上、業務改善活動に動き出しました」。
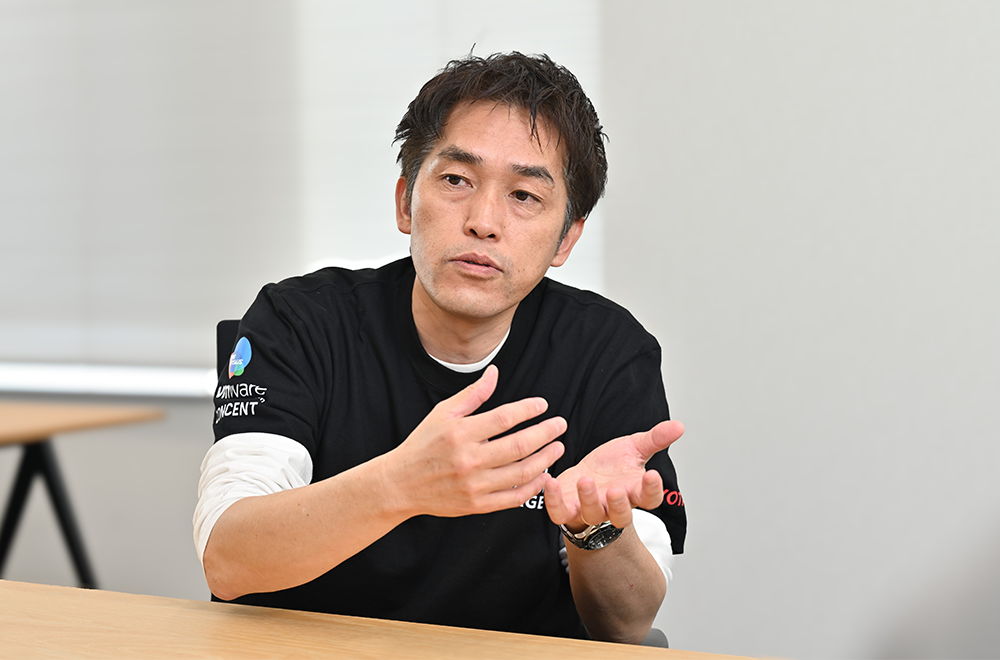
寺倉氏ら有志4人は「もっといいクルマをつくり、お客様に新しいよろこびをお届けする」という強い思いをトップとの間で共有。2022年10月に生産技術部傘下に「ものづくりデジタル推進部」が設立された。2024年1月にはものづくりデジタル推進部を中心に、社内に点在していたDXやITに関わる部署を統合。2025年1月に社長直轄組織「デジタル変革推進部」が誕生した。
トヨタ車体のDX活動のベースにあるのは、TPS文化だ。デジタル活動方針では、「みんなのために」「TPS + デジタル」「全員参加」の3つが柱となっている。
デジタル変革推進部が定めたデジタル化の進め方は、
STEP1.TPSの実践で得た膨大な紙情報や暗黙知のデータ化
STEP2.現状把握(見える化)
STEP3.データ分析・解析
STEP4.対策(最適化)
の4プロセスを踏む。トヨタ車体におけるDXは「現場、現物、現実」の3現主義の観点から、現場主導によるボトムアップで進められている。
成功モデルの1つが、トヨタ車体 吉原工場 塗装部の品質向上に向けた取り組みだ。「可視化とデータ分析」を活用し、慢性的不具合の要因特定・改善に挑んでいる。選択したのはウイングアークのBIツール「MotionBoard」だ。
「可視化とデータ分析」を活用し慢性的不具合をなくす
どこから現場主導のDXに取り組むべきか。吉原工場 塗装部はウイングアークと電通総研より、電通総研のDX診断サービス「工場ドック※」を受けた。塗装工場全体に対し、デジタル化の進み具合や紙帳票による業務範囲などの診断、現場のヒアリングなどをもとに点数をつけ、他社との比較も加えたレポートを提出。その結果、デジタルによる品質向上が重点テーマとして浮かび上がってきた。
「工場ドック」の結果を受けて、吉原工場 塗装部 技術員室 主任 畑中 啓佑氏は、塗装部のDX担当としてさまざまな展示会に出向き、デジタルによる品質向上に向けたアイデアを探した。気づいたのは、これまで要因がつかめなかった「慢性的不具合をなくす」ために、客観的な分析ツールを活用するというアプローチだ。ツール選びのポイントについて畑中氏は話す。
「データベース、可視化、分析がワンパッケージとなっていることを重視しました。個別ツールでは、それぞれにスキルを必要とし、データ連携にも手間がかかります。現場で使う観点から、ワンパッケージに加え、伴走型サポートも必須でした。すべてを満たしていたのがウイングアークのMotionBoardでした。『工場ドック』の取り組みとも方向性が一致していたことで、吉原工場 塗装部としてMotionBoardを使って『慢性的不具合をなくす』取り組みにチャレンジしたいとデジタル変革推進部に相談しました」

寺倉氏は、「吉原工場 塗装部のチャレンジは、全社のデジタル活動方針やデジタル化の進め方と合っていました。ITインフラやリソースなどのアセットをフルに使って構わないし、外部のサポートも受けて成果を出してほしいと伝えました」と話し、こう付け加える。「デジタル変革推進部のスタッフも吉原工場 塗装部のプロジェクトに参加しました。現場主導によるDXですが、進めやすいようにしっかりサポートするためです」。
伴走型サポートのもと「データを見抜く力」を習得
トヨタ車体の防錆塗装工程は、車体工程で組み上げたものを、洗浄して油分を落とし、塗装して洗浄し、乾燥炉で焼き付けるといった2時間を要する作業だ。慢性的不具合について畑中氏は説明する。
「塗膜(塗装を塗って乾燥させた膜の層)に付着する“もの”や“要因”は多岐に渡ります。現象が出た段階で要因を特定するのは難しいため、慢性的不具合の対応に苦慮しています。データを収集・分析し、起こり得る不具合を把握し対策を講じることで不良率を削減できると考えています」
2023年10月、ウイングアークの伴走型サポートのもと、吉原工場 塗装部はMotionBoardを使った慢性的不具合改善プロジェクトをスタートさせ、防錆塗装作業の全20工程に関して測定値やセンサーデータを抽出し、データの粒度を合わせ、ウイングアークのデータ分析基盤Dr.Sumに収集・蓄積。それらのデータをもとに1種類の不具合にターゲットを絞り分析を実施した。
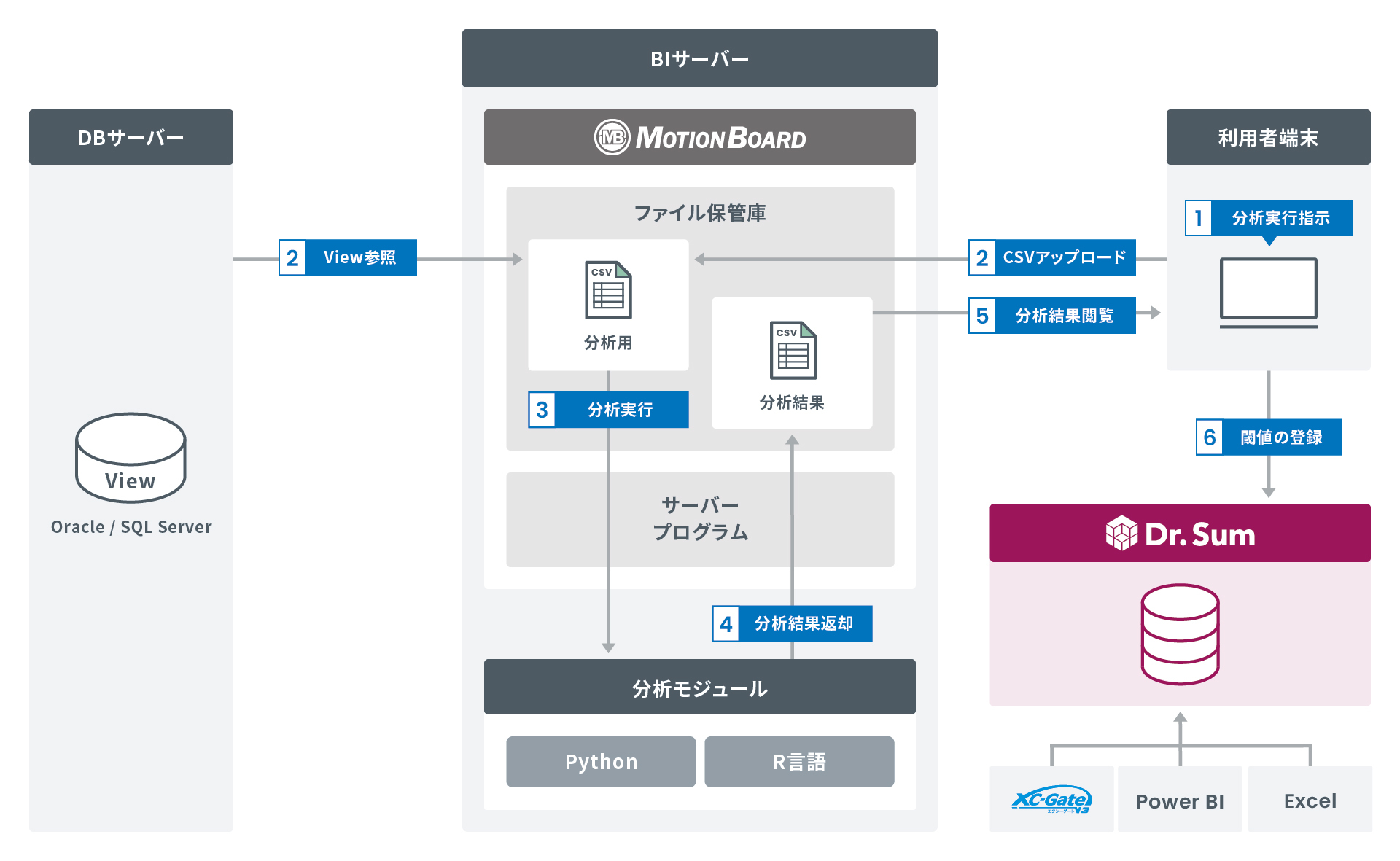
ここでは、MotionBoardに標準搭載されている機械学習の代表的手法「ランダムフォレスト」および「決定木」を利用した。収集・蓄積したデータに対し、不具合情報を付加することで、良品と不良を分ける分析モデルを作成。その結果を統計グラフで視覚化することにより変化点が見えてくる。
MotionBoardの分析機能により、項目を切り替えるだけでスピーディに分析の考察ができる。ポイントは、データからいかに価値を導き出すか。現場の知識や知見とともに、統計解析やデータ活用の知識が必要だ。ウイングアークの伴走型サポートについて、畑中氏は評価する。「ウイングアークのデータサイエンティストは、ヒストグラム(統計グラフ)の見方など、初心者の私に『データを見抜く力』を丁寧に教えてくれました。今後、実践の中で私が学んだことを、まずは技術員室の中で広めていきたいと思います」。
特定不具合の不良率40%削減、データ分析対象を拡大
分析結果により、従来の管理範囲に比べて精度の高い管理値(閾値)を導き出すことができた。その管理値を運用ラインに適用し、該当不良に関して不良率40%削減(従来比)を実現。また、設備のメンテナンス情報などと照らし合わせながら変化点を見ることができる運用画面の実装により、メンテナンスの良し悪しの判断を素早くできる。
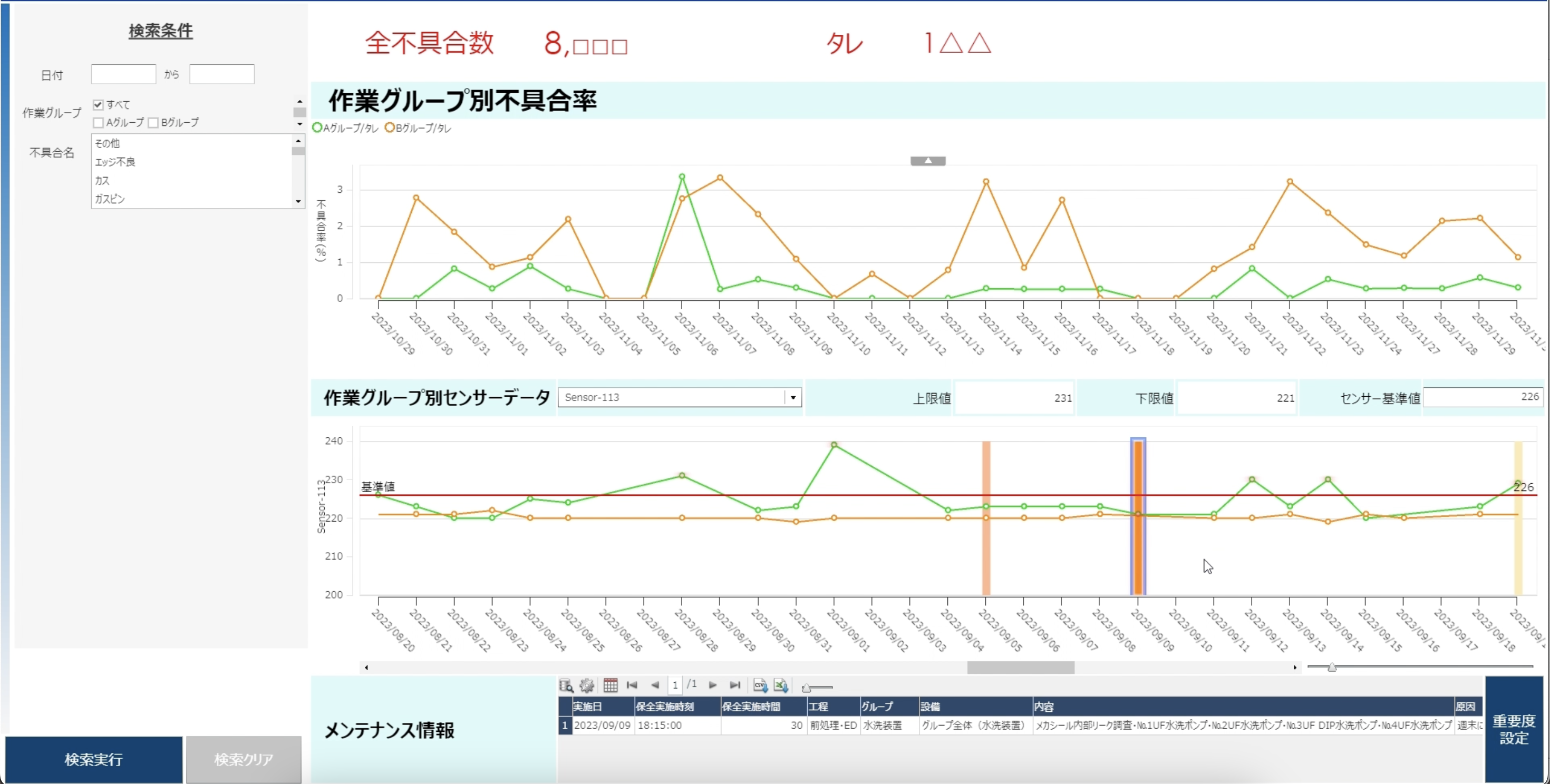
今後の展開について畑中氏は話す。「今回、1種類の慢性的不具合に対して効果が出たことで、『この不具合の要因も特定できないか』といった声が寄せられています。人材を育てながら、慢性的不具合をなくすために取り組みを進めていきたいと思います」。
現場においてデータ分析の利用が拡大するほどに、均一化が課題となる。これを解決するべく、ウイングアークは分析結果の比較や要約を、AIが行う機能を準備している。畑中氏はAI活用に関してウイングアークへの期待を述べる。「設定した閾値を超えた場合、MotionBoardはアラートを発信します。不具合が発生した際に、AIアシスタントが現場の組長をサポートするといった機能があると、『判断とアクション』のスピードアップが図れると思います。ポイントは、AIの出した結果を鵜呑みにするのではなく、『最終判断はヒト』が行うということ。AIを活用したカイゼンでは重要になると考えています」。
現場で分析し、その結果を現場で生かす。MotionBoardはTPSとの親和性が高い。「吉原工場 塗装部のMotionBoardを活用した取り組みは、トヨタ車体のDX活動における成功モデルになると思っています。大事なのは、現場にデータ活用文化を定着させていくことです」(寺倉氏)。
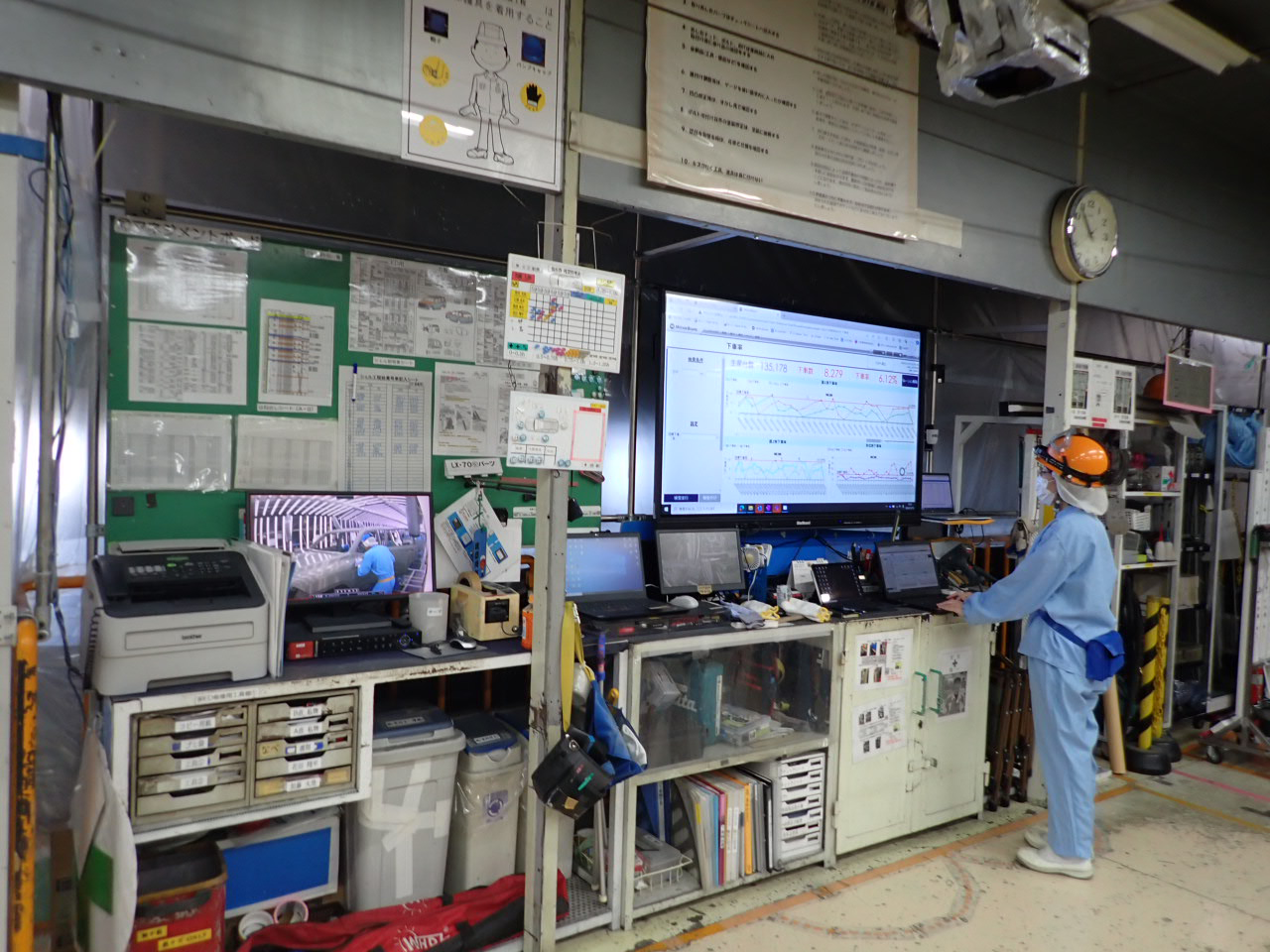
デジタル変革推進部は、デザイン思考演習、DX人材育成など“学び”にも力を入れている。自律的に考え、行動するために、スキルアップとマインドチェンジを促すためだ。「人に寄り添うクルマづくりで、もっと暮らしを豊かにしたい」というトヨタ車体の思いを実現するために、ウイングアークはMotionBoardを通じてカイゼンの進化を支援していく。
※株式会社電通総研のDX診断サービス「工場ドック」
https://mfg.dentsusoken.com/solution/smart-factory/iot/factory-doc.php
Company Profile
トヨタ車体株式会社
設立:1945年8月31日
本社所在地:愛知県刈谷市一里山町金山100番地
主な事業内容:トヨタ車の企画・開発・生産
URL:https://www.toyota-body.co.jp/
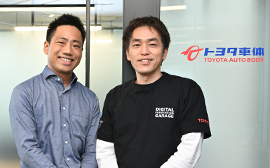
(写真左より)
吉原工場 塗装部 技術員室 主任 畑中 啓佑 氏
デジタル変革推進部 主査 兼 商用営業部 主査 寺倉 隆治 氏
導入製品
MotionBoard
様々なデータを統合・可視化するBIダッシュボード。統合・可視化にとどまらず、データ入力や柔軟な画面設計で業務に必要なアプリケーションをノーコードで作成可能。
Dr.Sum
あらゆるデータをリアルタイムに収集・蓄積・分析する、データベースエンジンを軸としたデータ分析基盤。10億件のデータも1秒台で集計する超高速集計を実現。