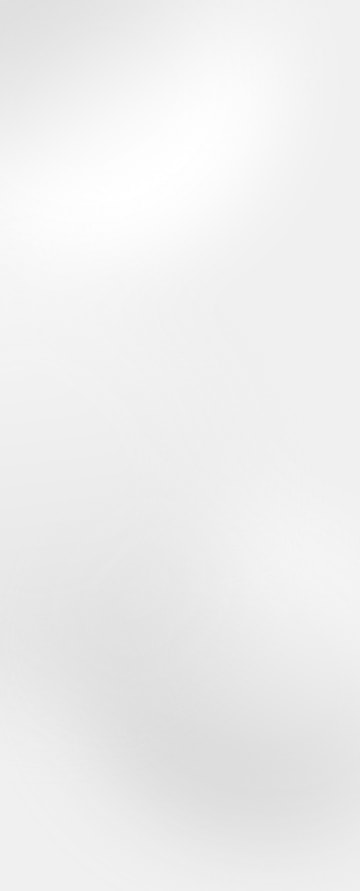
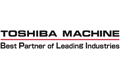
東芝機械株式会社
IoTとの連携で自律協調型の工場経営を実現
生産情報の“見える化”による現場改善
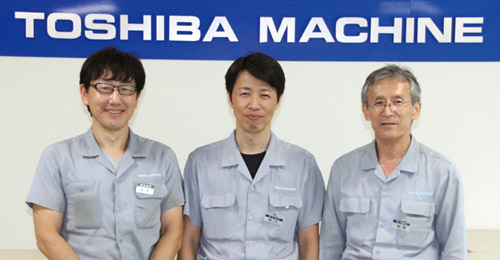
- 製品
製造業に対する要求が、従来の「モノ」からプラスアルファの価値をもった「モノ+コト」に急速に変化してきた。そうした中で東芝機械株式会社(以下、東芝機械)は、総合機械メーカーとして長年にわたり培ってきた技術と経験を活かし、IoTでデータを収集、集めたデータを分析し、スマートファクトリーに対応する「IoT+mプラットフォーム」を開発。外販拡大を見据え、社内のさまざまな工場での実証を進めている。
その最先端で活動する材料加工事業部は、ウイングアークのMotionBoardをベースに多様な生産情報の見える化を実現した。複数のExcelシートに分散していた情報を1つのダッシュボードに集約するとともに、IoTで収集した機械や装置を集約するとともに稼動データをダッシュボードに連携し、モニタリング。現場の知恵と経験を改善活動につなげ、自律協調型の工場経営を目指している。
導入背景
班別進捗状況、機械別操業達成率、ラインの負荷情報、品質情報の4つのカテゴリの生産情報をExcelで管理していたが、これらの情報を横断的に見るのは困難で、状況変化への対応が遅れていた。また、各ラインの担当者が加工・集計した二次情報が社内に散在し、必要な情報を探し出すのに手間取ったり、類似のレポートを何人もが作成したりするなど非効率な作業が発生していた
- 課題
-
- 経営情報の見える化ツールとして情報システム部門が先行して導入していた
- 全社共通のIT 基盤として展開したい
- 解決策導入ポイント
-
- 複数のExcelシートに分散していた生産情報を1つの画面に集約
- 直感的に誰でも認識できるダッシュボードを作成
- 効果
-
- 生産状況がリアルタイムで把握
- 現場の“ 気づき”が改善を促し毎月の生産性を着実に向上
- IoTダッシュボードとの連携で機械の停止時間を半分以下に削減
Excelで個別に管理されていた多様なデータを一つの画面に集約し、誰もが直感的に操作・認識できるダッシュボードを実現。ラインごとの実績と達成率、予算の消化など生産状況をリアルタイムに把握できるようになったことで、各班が品質改善や生産性向上に向けて切磋琢磨しあう競争意識を芽生えさせている
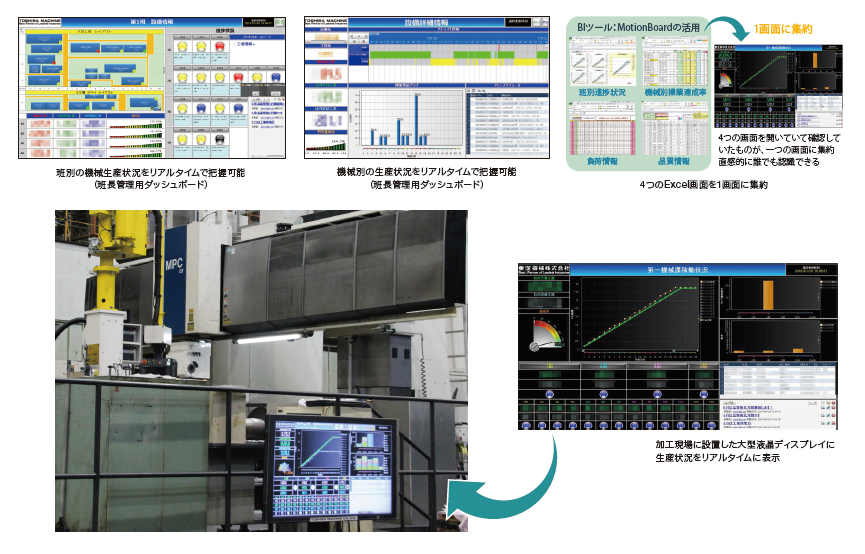
製造業に付加価値を生み出す「IoT+m プラットフォーム」を提案
東芝機械は、自動車、エレクトロニクス、光学、ナノテクなどの産業分野で用いられる射出成形機、押出成形機、微細転写装置、精密機器、工作機械、電子制御装置、産業用ロボットなど幅広い装置を手掛け、中でもダイカストマシンに関しては世界でトップクラスのシェアを有する総合機械メーカーだ。
しかし、グローバル競争が激しさを増し、機械単体での差別化が難しくなっており、いかなる付加価値を打ち出せるかが問われている。そうした中、新たな重点戦略の一つに位置付けているのがIoT(Internet of Things)への取り組みだ。
同社 制御システム事業部 制御システム技術部技監の前原弘之氏は、「東芝機械グループは総合機械メーカーとして多岐にわたる機械の豊富な知識と経験を有しています。特に制御装置については自社開発を行っており、生産現場に密接したトータルなIoT の提案が可能です」と、自社のポテンシャルの高さを示す。
そして開発を進めているのが、「IoT+mプラットフォーム」と呼ぶ工作機械IoT 活用ソリューションだ。「ゼロダウンタイムを目指して突発故障を未然に察知」「新規のみならず既存設備も含めた機械の状態を可視化」「スマートファクトリー化に対する課題を顧客との共創で解決」という3つのコンセプトに基づいたIoTを指向している。
IoT基盤の運用を支える生産情報の見える化
将来的に幅広い産業への外販を目指す「IoT +mプラットフォーム」だが、その大前提として東芝機械がまず注力しているのが、社内工場における実証だ。
「自社工場内では長寿命の大型機械製品も運用しており、予防保全に適した豊富なサンプルを収集することができます」と前原氏は語る。こうした現場/ 実務レベルの事例から得られた知見とノウハウをパッケージ化/ テンプレート化し、自社製品に組み込むほか顧客に提供するサービスにも反映していく狙いだ。
制御システム事業部が開発したIoT の共通基盤を国内の主要工場に展開し、実証をスタートさせているが、中でも先行しているのが材料加工事業部だ。大型工作機械で用いられるさまざまな部材を鋳造から仕上げまで一貫生産している加工現場である。
温度、湿度、振動、周波数、色などの多様なセンサーからデータを集めてリアルタイムにモニタリングする「スマート見える化」(監視IoT)をベースに、集めたデータを分析することで「スマートメンテナンス」(保守IoT)や「スマートマニュファクチャリング」(製造IoT)につなげていくトータルなプラットフォームを構築した。
そしてこのIoT 基盤の運用を支える、もう一つの重要な要素として整備を進めているのが生産情報の見える化を実現する仕組みだ。
同事業部の副事業部長を務める桧作 秀文氏は、「生産計画や品質改善に関する多様なデータを見える化し、現場の知恵と経験を改善につないでいくことで、最終的には自律協調型の工場経営を実現したいと考えています」と構想を語る。
もっとも生産情報の見える化はいまになって始まったわけではなく、10年以上も前から取り組んできたテーマだ。そこにはどんな課題があったのだろうか。
材料加工事業部では、大きく「班別進捗状況」「機械別操業達成率」「ラインの負荷情報」「品質情報」の4つのカテゴリの情報をKPIとしてExcelで管理し、関係者に公開することで見える化を行ってきた。だが、これらの生産情報を横断的に見るのは困難で、全員が共通の認識を持つことができず、どうしても状況変化への対応が遅れてしまう。また、「Excelの公開情報をもとに各ラインの担当者が加工・集計した二次情報が社内に散在し、必要な情報を探し出すのに手間取ったり、類似のレポートを何人もが作成したりするなど非効率な作業が発生していました」と桧作氏は語る。
4つのExcelシートに分散していた生産情報を1つの画面に集約
本当の意味での生産情報の見える化を実現するためには、これまでExcelで個別に管理されている多様なデータを一つのダッシュボード上に集約し、誰もが直感的に操作・認識できるBIの仕組みが必要だ―。このように考えた前原氏と桧作氏が着目したのがウイングアークのMotionBoardである。
「もともとMotionBoardという製品自体は知っていましたが、SI パートナーのトーテックアメニティ(以下、TOTEC)に招待された展示会で初めてデモを見せてもらい、その画面の完成度の高さに驚きました。これなら私たちが望んでいる生産状況の見える化をイメージどおりの形で実現できると確信しました」と桧作氏は振り返る。また、「経営情報を可視化するツールとして、すでに情報システム部門がMotionBoardを導入していたことも大きなポイントです」と語るのは前原氏だ。
「BI 導入については『一部のアナリティクスだけでなく全社的に利用できるツールを』という基本的な考えがあり、すでに社内で実績のあったMotionBoardを最有力候補としていました。そこにタイミングよく材料加工事業部から相談を受け、迷わずMotionBoardを推奨しました。多様な生産情報を管理している既存のExcel をそのまま活かし、その上に“ かぶせる” 形でデータを統合できることも一押しした理由です」
こうして東芝機械は2017年4月、全社共通のBI基盤としてMotionBoardを拡大導入。材料加工事業部はTOTECの協力を得てプロトタイピング手法をベースにダッシュボード構築を進め、同年8月時点ですでに20以上の画面を完成させている。
例えば班長管理用ダッシュボードでは、それぞれの担当ラインの実績と達成率、予算の消化など生産状況をリアルタイムに把握することが可能となった。特に加工途中の各部品についてその進捗率を青(順調)、黄(注意)、赤(遅れ)のシグナルで表示し、迅速な対処を促している。さらにこの画面から機械別のダッシュボードを呼び出し、負荷状況や日々の稼働実績、工程ごとのマシンスケジュールなどを確認することも可能だ。
また、オフィスの目立つ場所に大型ディスプレイを設置。操業計画と実績、品質コスト、不良件数およびその内容など、材料加工事業部全体の生産状況をMotionBoardで見える化し、サイネージ表示している。
「このダッシュボードには、ライン別の生産実績や進捗状況も横並びでリアルタイムに表示しています。これがきっかけとなり班ごとの競争心が生まれてきました。他のラインに負けないように自分たちの生産性を高めるために何をすべきかを考えて行動する、お互いの向上心を刺激しあう現場レベルでの切磋琢磨が以前にも増して見られるようになりました」と、桧作氏は手応えを示す。
気づけば動く、動けば変わる生産現場の改善サイクルを確立
一方、スマート見える化(監視IoT)のダッシュボードには、工場内の各機械や装置の稼動状況、発生中のアラームなどが一覧表示される。この見える化による最大の成果は、「その時点で各ラインに発生している異常を察知するのはもちろん、時系列に基づいた長期的な傾向も捉えられるようになったことにあります」と桧作氏は語る。
例えば、期間を指定したトレンドグラフと起こった事象(イベント履歴)を紐付けて見ることも可能だ。見過ごしがちだった長期的な変化も捉えられるようにすることで、「現場が何かに気づき、気づけば動く、動けば変わる」という改善サイクルが確立される。
「生産情報のダッシュボードと監視IoT のダッシュボードを合わせて見ることで、毎月早い段階で生産計画に基づいた“ 備え” が行えるようになり、月々の生産性は着実に向上しています。また、見える化されたデータから『ある部品のちょっとした汚れが機械の故障につながっている』という“ 気づき” を得た現場が、自発的なクリーニングに乗り出すなど、さまざまなアクションにつながっています。この結果、ダッシュボードの導入前後で機械の故障停止時間は半分以下に削減しています」と桧作氏は語る。技術・品質本部 技術企画担当 主幹の青野 竜二氏も、「これは全社的に見ても画期的な品質改善、生産性向上です。ERP(基幹系システム)やMES(生産実行システム)などの基盤を大幅に変更することなく容易に導入し、多様なデータを現場主導で直感的に見える化できるMotionBoardだからこそ得られた成果と考えています」と評価する。
先述したように東芝機械では、この成果を自社製品のさらなる品質向上やブランド力の向上につなげていくとともに、新たな付加価値サービスとして生産情報の見える化を含めたトータルなIoT ソリューションの外販を進めていく考えだ。その意味でも今後求められるのが、データ分析のさらなる強化である。「IoT で収集した多様なデータの見える化については、かなりの精度で実用レベルに達することができたと自負しています。問題はその先にあり、見える化されたデータの判断を個人のスキルやセンスに依存している状況を変えていきたいと考えています。具体的には当社独自の解析・診断技術に加え、AI (人工知能)をベースにした分析技術も取り入れながら、ダッシュボードとの連携を進めていく計画です」と前原氏は語る。
東芝機械では2016年4月から新中期経営計画「TM-PΣ Plan」をスタートさせている。その中で、業界最先端の技術を指向する市場に向けて他社の追随を許さない機能を搭載した商品を提供する一方、搭載技術の汎用化が進んでいる商品については前後工程をシステムとして取り込み、生産ラインにおける自動化・省人化の提案を行うという基本方針を打ち出している。この新戦略の根幹を支えるのが、高付加価値を生み出すトータルなIoTソリューションに他ならない。世界の「ものづくり」に貢献する総合機械メーカーとしてさらなる成長を目指し、2018年度は連結売上高1,400億円、ROS(売上高経常利益率)6.5%以上、ROE(株主資本利益率)6%以上の達成を見込んでいる。
Company Profile
東芝機械株式会社
創業 :1938年12月
本社所在地 :静岡県沼津市
事業内容 :射出成形機、ダイカストマシン、押出成形機、印刷機械、工作機械、精密機器、微細転写装置、産業用ロボット、電子制御装置、鋳物などの製造・販売
URL :https://www.toshiba-machine.co.jp/jp/
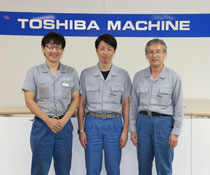
技術・品質本部 技術企画担当 主幹 青野 竜二 氏(写真左)
材料加工事業部 副事業部長 桧作 秀文 氏(写真中央)
制御システム事業部 制御システム技術部 技監 前原 弘之 氏(写真右)
導入製品
MotionBoard
様々なデータを統合・可視化するBIダッシュボード。統合・可視化にとどまらず、データ入力や柔軟な画面設計で業務に必要なアプリケーションをノーコードで作成可能。