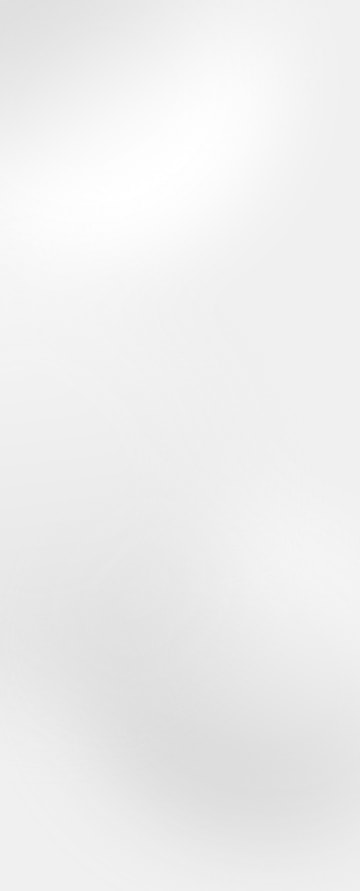
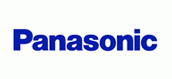
パナソニック株式会社 アプライアンス社
IoTを基軸に高品質・高効率の工場を目指して、4M3Hの変化点、生産進捗、品質データなど、製造管理指標を25項目にわたり一元的に見える化。
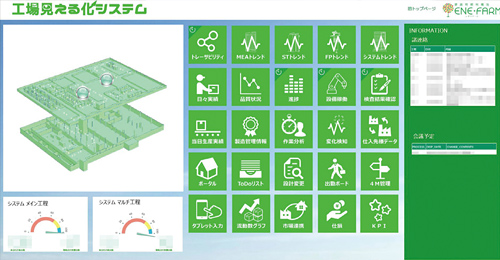
- 製品
- 業種
-
製造
パナソニック アプライアンス社では、家庭用燃料電池「エネファーム」の製造工程において、高品質・高効率を目指した工場IoTの導入に取り組み、その進化を加速させている。工場のあらゆるプロセスをつなぎ、デジタル化されたデータをMotionBoardで統合・一元管理することで、4M(Man、Machine、Material、Method)の変化点、生産進捗、品質データなど、全25項目の製造管理指標の見える化を実現。「人モノづくり」をはじめ、製品・工程設計力の向上、職人技の汎用化・自動化、バラつきのない尖った品質などをテーマとした生産革新と品質革新を推進している。
導入背景
例えば特定のパーツに設計変更が発生した際に、それにあわせて管理工程図や作業指図書がきちんと修正されているかどうか、現場の作業と紐づけてダイレクトに確認できる仕組みを作りたいと考えた。
- 課題
-
- 「人モノづくり」をベースとした工場 IoTへの取り組みを開始
- これまで紙の台帳で管理していたデータのデジタル化と見える化
- 分散していたスモールデータをビッグデータ化
- 解決策導入ポイント
-
- さまざまなデータソースと柔軟に連携したデータ入力が可能
- 製造現場が主導権をもって活用できる使い勝手の良さ
- 効果
-
- あらゆるモノとプロセスをつないだデータをリアルタイムに見える化
- いま起こっている変化点や工程異常に対して俊敏に反応し、アクションを起こす工場への変革を支援
品質、生産進捗や、4M3Hの変化点など全25項目に わたる製造管理指標をMotionBoardで一元管理し、リアルタイムに見える化するとともに、情報の変化を高感度に示す。この情報を製造現場で共有することで、いま起こっている変化点や工程異常に対して俊敏に反応し、アクションを起こすことが可能となった。
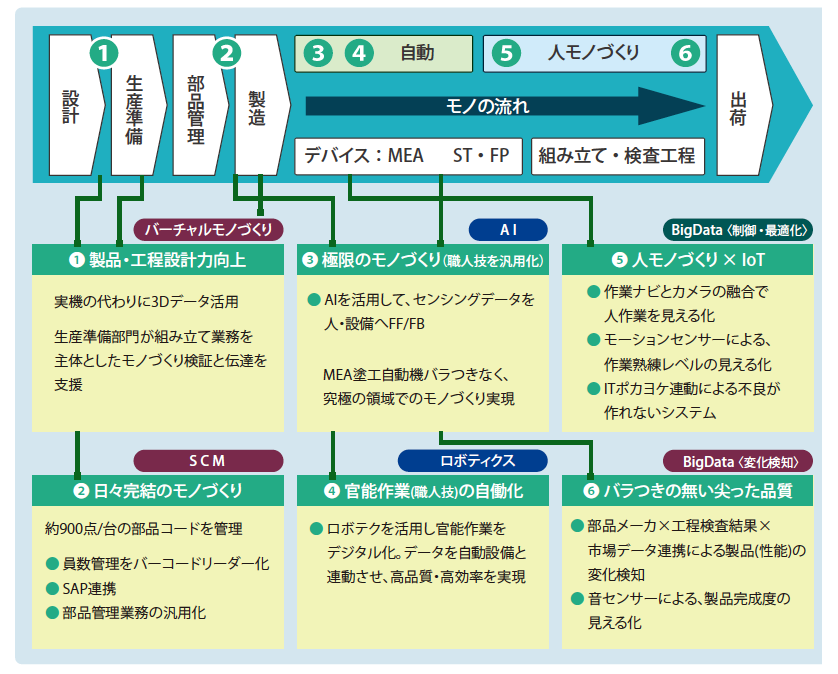
IoTは“魔法の杖”ではない
最終的には“人”が鍵を握る
都市ガスやLPガスなどの家庭用ガスを利用して発電すると同時に湯も沸かすことができる家庭用燃料電池「エネファーム」は、省エネ意識の高まりを背景に順調に需要を伸ばし、国内の普及台数は2017年に20万台を突破した。その半分以上のシェアを占めるのがパナソニック アプライアンス社だ。滋賀県の草津工場を拠点に、市場ニーズの高まりに応えるべく生産性をさらに高め、2019年度末までに累計20万台の生産を達成するという目標を掲げている。この計画を支える基盤として同社が注力しているのが、IoT(Internet of Things)の仕組みを活用した高効率・高品質工場の実現だ。
同社スマートエネルギーシステム事業部草津工場の工場長を務める高田 泰治氏は、「私たちは、各地域のガス会社様に向けたB2Bのビジネスモデルのもとでエネファームを展開しています。そうした中で、工場こそが最高のセールスマンだと考えています。デジタルによる見える化を追求した『現場密着のIT』の使いたおしと、AIやセンシングなどの技術を駆使した『先進のIT』の使いこなしを高度に融合させ、お客さまの期待を超える付加価値をもった商品を創り出す、究極の工場IoTを目指しています」と、その根底にあるモノづくりのポリシーを示す。
なお、同社が目指す「究極の工場IoT」とは、単にテクノロジーの導入や活用のみによって成し遂げられるものではない。IoTによって多様なモノから情報を収集することが可能となるが、一方でそこからどんなデータを、どのように集め、どう使うのかが問われることになるからだ。
高田氏は、「データの有効性を見極められるのは、対象となるモノを知り尽くした製造現場のプロフェッショナルのみです。どれだけモノのデータが増えても、それを使いこなせる人材が増えなければ、生産や品質の改革につなげていくことはできません。また、モノは簡単に増やしたり、改良したりすることが可能ですが、現場の人材は一朝一夕で育てることはできません」といった課題を挙げながら、「IoTは決して“魔法の杖”ではなく、最終的なデータ活用の鍵を握っているのは、やはり人なのです」と強調する。
こうしたことから同社がIoTへの取り組みのベースとしているのが、「人モノづくり」というコンセプトである。
4M3Hに関するデータを集約し、変化点を見える化する
工場における生産性や品質は、「Man(作業者)」「Machine(機械設備)」「Material(原材料)」「Method(作業方法)」のいわゆる“4M”の要素の組み合わせによって決まる。また、「初めて」「変更」「久しぶり」の“3H”に起因するヒューマンエラーを削減することで、効率を高めることができると考えられている。
2015年、同社草津工場における「人モノづくり」をベースとしたIoTへの取り組みは、まずこの4M3Hに関するデータを集約し、その変化点を見える化することから始まった。「例えば特定のパーツに設計変更が発生した際に、それにあわせて管理工程図や作業指図書がきちんと修正されているかどうか、現場の作業と紐づけてダイレクトに確認できる仕組みを作りたいと考えました」と高田氏は振り返る。
その基盤として導入したのが、ウイングアークのMotionBoardである。パナソニック社内ではすでに多くのBI製品を活用しており、それぞれの拠点や業務で高度なデータ分析の成果も上げているが、そうした中で今回はなぜMotionBoardだったのか。草津工場 製造二課の課長を務める西久保 正美氏は、次のように語る。
「私たちがMotionBoardを選んだ最大の理由は、データ入力が最も容易なツールだったことです。4M3Hをはじめ生産実績や進捗状況、品質に関するあらゆるデータを私たちはこれまで紙の台帳で管理していました。まさにゼロからスタートしたデジタル化への取り組みであるだけに、製造現場のメンバー自身による試行錯誤を通じて、究極の工場IoTに対する思いをダッシュボードに体現できるMotionBoardの使い勝手の良さに、他のBIツールにはないメリットを感じました」
バラツキのない尖ったモノづくりとして職人技の汎用化を目指す
その後、「人モノづくり×IoT」の取り組みは分析/制御や最適化(標準化)を実現するフェーズに入り、「不良が作れない」ことを狙いとする「作業ナビゲーション」と呼ばれるシステムが作られた。
もともと作業ナビゲーションは、各工程の担当者に対して次に実施すべき作業の手順を音声や画面で指示するなど作業のアシスト“補助”を行うこと目的として開発され、2009年頃から運用されてきたものだ。これをさらに作業の“保証”を行うものへと進化させたのである。
例えばクィックファスナーの挿入治具は、今までは挿入治具と挿入確認治具(ポカヨケ)を使用し6つの手順で作業を実施し、気遣いし作業をしていたのを、何とか生産性向上と更なる品質の担保をしたいとのことから、ワンアクション、ワンチェックの思想で、クィックファスナーの挿入と同時に確認もできる新たな治具(ITポカヨケ)を開発し作業ナビゲーションとの連携を実施し、IoTの利活用を進化することができた。又電動ドライバーと作業ナビゲーションとの連携も進めながら、更なる品質の尖った商品に仕上げていっている。
「あらゆる工程の作業を標準化し、その確実な実施をIoTによって見届けることで、品質のバラツキをなくします」と高田氏は強調する。
さらに作業ナビゲーションはビデオカメラとも連動し、作業者の“動き”を映像データとして一定期間保管している。「万一、製品に品質異常を検知した際には、作業ナビゲーションの時間軸に基づいて映像データをトレースし、その時にどんな作業が行われたのかを分析することで真因を究明します」と西久保氏は語る。
これは、不良を起こした作業者を特定するための監視を狙いとしているわけではない。作業者に無理な姿勢を強いている作業操作や非効率な手順を検証するなど、目的はあくまでもその工程に潜んでいる問題を明らかにし作業改善することにある。同時に熟練作業者のお手本となる動きも分析するなど、多角的な観点から生産性の継続的改善活動につなげているのである。
また、工程の「バラツキのない尖ったモノづくり」に向けて、職人技を汎用化するというチャレンジも開始した。草津工場 製造一課の課長を務める吉野 強氏は、「職人の動きをセンシングしたデータをAI手法で分析し、そこから得られた学習モデルを各プロセスや設備にフィードフォワード/フィードバックすることで、高度な熟練を要していたMEA塗工作業などの自動化を実現したいと考えています」と構想を示す。
すべてのプロセスをつないだデータをリアルタイムに見える化する基盤へ
さらに、同社が2018〜2019年度に向けて進めているIoTの全体計画を俯瞰してみよう。
設計および生産準備のプロセスでは、製品・工程設計力の向上を目的とした「バーチャルモノづくり」の取り組みが始まった。VPS(Virtual Product Simulator)を導入して3D-CADと作業ナビゲーションの連携を図り、生産準備部門が組み立て業務を主体としたモノづくりの検証と情報共有を支援するものである。
職人技のデジタル化(汎用化)に関しては、先述のバラツキのない尖ったモノづくりに加え、ロボティクスを活用した官能作業の自動化にも着手している。IoTで収集したデータを自動設備と連動させることで、例えば精密な材料計量や混合回転条件などが求められるインク作成を最適化し、高品質・高効率化を実現することが考えられている。
組み立ておよび検査工程においては、製品のバラつきのない尖った品質」の追求が行われている。ひとつの事例として、振動センサーによる製品完成度の見える化が実施されている。これまでも完成品に対して人による官能検査は行われてきたが、NG/OKの微妙な判断にはどうしても人によるバラつきが生じてしまう。そこで振動センサーで収集したデータをもとに、分析し客観的かつ高精度な検査を実現する。
今後は、部品メーカーから提供されるデータと工場のビッグデータ、さらに市場と連携させ、更なる製品完成度の見える化/最適化等が計画されている。
これによって同社のIoTへの取り組みは、設計から出荷に至るすべてのプロセスをカバーすることになる。そして、そこから発生するすべてのデータを集約するMotionBoardのダッシュボードは、現在では100以上のボードから構成される
「草津工場見える化システム」へと発展している。「品質、生産進捗や、4M3Hの変化点など全25項目にわたる製造管理指標を一元管理し、リアルタイムに見える化するとともに、情報の変化を高感度に示します。この情報を製造現場のメンバーは、責任者層も参加する日々のミーティングで情報を共有し、情報に基づく迅速かつ的確な判断や、発生している問題点の対応策をフォローします。この見える化システムを最大限に活用することで、いま起こっている変化点や工程異常に対して俊敏に反応し、アクションを起こす工場への変革を図ります」と高田氏は語る。お客様から「工場が変わったね!」と言われ続けることが、工場の価値を最大化するという理念のもと、同社は2020年以降の将来に向けても草津工場を新たな顧客価値創造の拠点として位置づけ、未知の進化にチャレンジしていく考えだ。
昨今、日本の多くの製造業が深刻な人手不足に直面しており、高齢化が進む熟練工がリタイアしてしまったあと、どうやって現在の生産性や品質を維持するのか。一日も早くこの手立てを講じることが求められている。そうした中でこれまで匠の領域とされてきた熟練工の技をデジタルで汎用化し、次の世代に継承可能な資産に変えていく同社の取り組みは、この課題の解決策としても注目されるところだ。
Company Profile
パナソニック株式会社 アプライアンス社
設立 :2012年1月1日
所在地 :滋賀県草津市
事業内容 :パナソニックの社内カンパニーとして、空調・調理・家事・美容家電から店舗向けショーケースや自動販売機、燃料電池などの業務用デバイスまで、人々の豊かで快適 なくらし、快適な社会に貢献する商品を提供。
URL :https://panasonic.co.jp/ap/
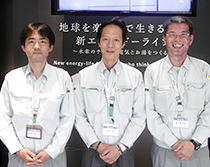
スマートエネルギーシステム事業部 草津工場
工場長 高田 泰治 氏(写真左)
製造一課 課長 吉野 強 氏(写真中)
製造二課 課長 西久保 正美 氏(写真右)
導入製品
MotionBoard
様々なデータを統合・可視化するBIダッシュボード。統合・可視化にとどまらず、データ入力や柔軟な画面設計で業務に必要なアプリケーションをノーコードで作成可能。