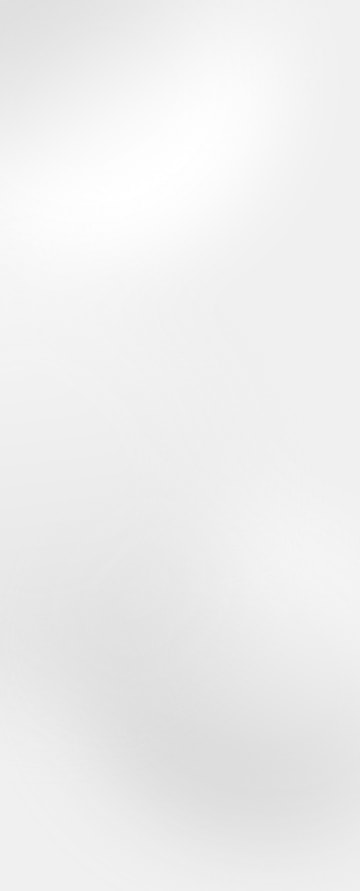
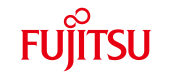
富士通アイ・ネットワークシステムズ株式会社
紙に記録していた進み遅れの状況をデジタル化。
部品の受入検査工程、スマートメーター用通信ユニットの組立工程でリアルタイムな可視化を実現。スマートファクトリー化に取り組む。
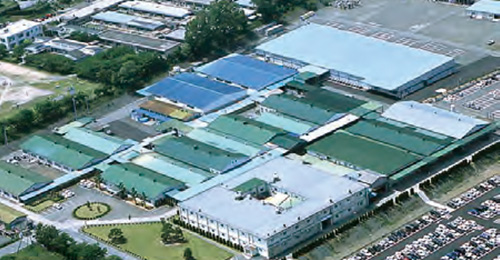
- 製品
- 業種
-
製造
設計・製造、品質保証、カスタマイズ・サービスまでワンストップでソリューションを提供する富士通アイ・ネットワークシステムズ(FINET)は、工場のスマート化を見据え、これまで人手に依存していた様々な工程の可視化に着手した。その基盤としてMotionBoardを導入。部品の受入検査工程で効果を実証することを手始めに、スマートメーター用通信ユニットの組立工程における生産状況のリアルタイムな可視化にも着手している。さらに今後は、より広範なラインへの横展開を進めていく計画だ。
導入背景
部品の受入検査では、翌週分の着荷予定データを木曜日に受け取ってExcelで集計し、前日に作業計画を立ててA3の紙に書き出していた。しかし、この紙の作業計画に示されているのは着荷の件数のみで、1件あたりに何個の部品が含まれているのかがわからず、また部品ごとに検査に要する時間も変わる。さらに週の後半になると着荷予定データの鮮度が落ちて、実際の着荷件数とのズレが大きくなってしまう。
- 課題
-
- 人手に依存していた工程管理をリアルタイムに可視化したい
- 紙に記録していた進み遅れの状況をデジタル化したい
- 解決策導入ポイント
-
- 製造業において多くの実績があり日本ではデファクトスタンダードとなっている
- 現場で使いやすいダッシュボード
- 効果
-
- 部品の受入検査に常時投入していた作業者を3人から2人に削減
- 製造現場の期待に近い可視化を実現
MotionBoardで開発したダッシュボード上には、前日に計画された作業工数を示す棒グラフと、ハンディターミナルで収集した作業実績を示す棒グラフが並べて表示され、リアルタイムに変化していく。その日に入庫しなければならない納品オーダー数に対する現時点の進み遅れをひと目で確認できる仕組みだ。これによって実現したのが、部品ごとにバラツキが生じていた検査・入庫作業の工数の平均化であり、結果として、従来は常時3名配置していた作業者を2名に削減できた。
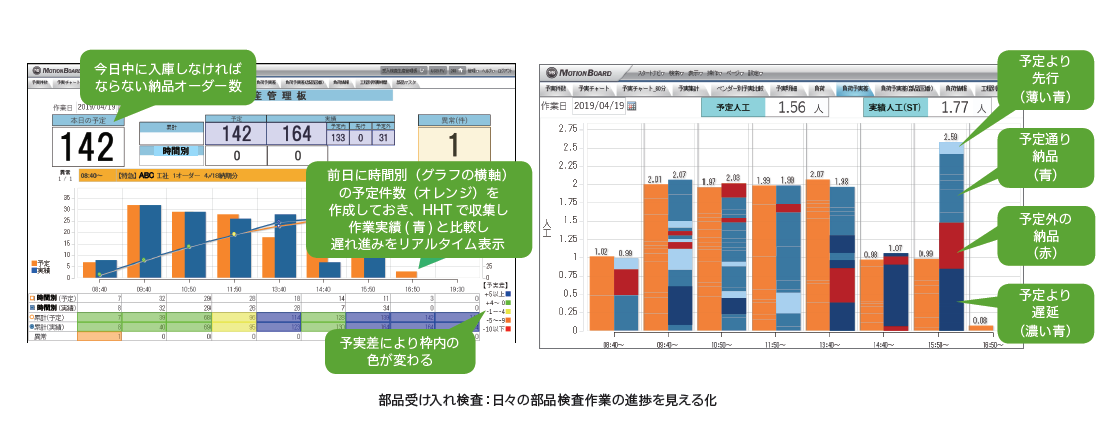
アンドンをデジタル化して広範な情報を可視化する
周囲三方に南アルプス、八ヶ岳、富士山を見晴らす豊かな自然に恵まれた山梨県南アルプス市に富士通アイ・ネットワークシステムズの本社と主力工場がある。1960年以来、半世紀以上にわたり高度ネットワークソリューションを提供。
ルーターやスイッチ、電力会社向けのスマートメーター用通信ユニットなどの製造を担う、富士通グループにおけるネットワークプロダクトの生産拠点である。さらに近年では、こうしたモノづくりに加え、国内・海外の各種ネットワーク製品への出荷保証や顧客ごとのカスタマイズのニーズに応えるマルチベンダーハブ&サービス(MVHS)を提供するなど、モノとコト(サービス)を融合したソリューションプロバイダーとして進化を続けている。
そしてその先に同社が見据えているのが工場のスマート化である。工場内の様々な製造装置、生産管理システム、各種センサー、製造実行システム(MES)などをデジタルでつなぎ、生産活動の自動化・自律化、サプライチェーンの統合などを実現するものだ。
そのためには、これまで人手に依存してきた工程を可視化することが第一歩となる。同社 ビジネスソリューション部 部長の武井 尚也氏は、「生産ラインに起こっている異常や様々な問題を現場のリーダーにランプの色の変化で伝える『アンドン』と呼ばれるシステムがあり、当工場でも広く活用しています。このアンドンをデジタル化し、より広範な情報をリアルタイムに可視化していくことが私たちの基本方針です」と語る。
では、その仕組みをどうやって実現するのか―。
インターネットをはじめ多方面から情報収集を続ける中でたどり着いたのがウイングアークのMotionBoardだ。同社 ビジネスソリューション部 システム推進の篠原 誠氏は、「2017年6月に訪れたウイングアークの展示会で、マウンタ(プリント基板へのパーツの実装機)の信号をMotionBoardで可視化した事例もあると聞き、興味を持ちました。デモで見たダッシュボードも、私たちが作りたいと思っていたイメージと非常に近いと感じました」と語る。
こうして同社はMotionBoardの導入を決定。「スクラッチ開発することも考えましたが、時間を浪費するばかりです。スピード感を重視するならMotionBoardを活用するのが最善と判断しました」と武井氏は語る。
部品の受入検査における実践
着荷から荷捌き、検査、入庫までの一連の作業を可視化
同社がまず開発に着手したのが、部品の受入検査を可視化するダッシュボードである。同社がサプライヤー各社から調達している約6,000種の電子部品や機構部品について、着荷から荷捌き、検査、入庫までの一連の作業を対象とするものだ。同社 製造統括部 製造部 部品 担当課長の山口 良和氏によると、それらの工程には次のような課題があった。
●着荷
各サプライヤーから調達した部品は、運送会社を使って送られてくるため正確な到着時間が分からない。加えて運送会社の搬入実績集計にも時間がかかる。
●荷捌き
事前の計画に沿って荷捌きを行っているが、実際の負荷に応じて所定の時間内に処理することが困難な場合もある。
●検査
部品の納入予定や実績をリアルタイムに照合することができず、未検収品の調査などにも時間がかかる。
●入庫
ライン外からの応援/ 退出のタイミングをタイムリーにコントロールできない。結果として過剰な人員の投入や、人手不足による残業が発生する。
このような問題が発生する原因は、作業の詳細を現場で把握しきれず、工場側も進捗状況をリアルタイムに管理できないことに尽きる。「翌週分の着荷予定データを木曜日に受け取ってExcelで集計し、前日に作業計画を立ててA3の紙に書き出します。しかし、この紙で示されているのは着荷の件数のみで、1件あたりに何個の部品が含まれているのかが分からず、また部品ごとに検査に要する時間も変わります。さらに週の後半になると着荷予定データの鮮度が落ちて、実際の着荷件数とのズレが大きくなってしまいます」と山口氏は明かす。
常時3名配置していた作業者を2名に削減
上記のような課題をMotionBoardでどのように解決したのだろうか。まず基幹系の購買システムで管理されている着荷予定データのほか、PCで管理している作業計画、作業現場のハンディターミナルから収集した実績などのデータを、MotionBoardをベースに新たに構築した部品間接検査システムに直接投入することにした。これにより常に鮮度の高い着荷予定データを基に作業計画を立てるとともに、その作業の進捗状況を厳密に管理できるようになった。
ダッシュボード上には、前日に作成された検査する予定の作業工数を示す棒グラフと、ハンディターミナルで収集した作業実績を示す棒グラフが並べて表示され、リアルタイムに変化していく。その日に入庫しなければならない納品オーダー数に対する現時点の進み遅れをひと目で確認できる仕組みだ。
これによって実現したのが、部品ごとにバラツキが生じていた検査・入庫作業の工数の平均化であり、「結果として、従来は常時3名配置していた作業者を2名に削減することができました」と山口氏は強調する。
また、計画作業を大幅に省力化できたことも大きな成果だ。先述したように、同社はExcelで集計された着荷予定データを基に翌日の作業計画を立てて紙に書き出していたが、この作業には30~60分程度の時間がかかるため、本来の担当ラインでの通常作業を終えた後で行うことになる。「現在はほぼ自動的に最新データがMotionBoardに反映され可視化されるので、準備に手間がかかりません。おかげで担当者の残業をなくすことができました」と山口氏は語る。
スマートメーター用通信ユニットの組立ラインにおける実践
システム開発工数の削減やリアルタイム表示を実現したい部品受入検査における実績と成果を踏まえ、同社は工場内のさまざまなラインや工程、関連業務へのMotionBoard の横展開を順次進めている。そして新たにトライアルを開始したのが、スマートメーター用通信ユニット組立ラインでの活用である。
スマートメーターとは、電力使用量の検針を自動化するデジタル式の電力量計で、同社はその通信ユニットの製造を担っている。電力各社はHEMS(住宅用エネルギー管理システム)の実現を目指す中で、従来のアナログ式の電力量計をこのスマートメーターへと急ピッチで置き換えを進めており、現在では山梨工場の主力製品の一つとなった。
このスマートメーター用通信ユニットの組立ラインにMotionBoardを導入することには、どんな狙いがあるのだろうか。同社 製造統括部 製造部 スマート製造課の課長を務める宇津江 賢一氏は、以下のように語る。
「スマートメーター用通信ユニットの組立ラインでは、進捗と異常を管理する台帳および試験機からのログを収集し、出来高管理、作業性分析、品質管理を行っています。これまでは手作業で組立を行う『マニュアルライン』3ライン体制で製造を行っており、ライン別の管理を実施していました。
そこに2018年に『自働化ライン』が2ライン追加され、トータル5ラインの生産体制へと増強されました。これに伴いラインごとの管理だけでなく、ライン全体を俯瞰した可視化が必要となったのです。また、自働化ラインからのログの収集は、マニュアルラインにおける人によるデータ収集とは方法や内容がまったく異なるため、データをどのように集計するのかといった点でも苦労していました。そこにMotionBoardを活用して可視化を行うことで、システム開発工数の削減やリアルタイム表示を実現したいと考えました」
異常が発生した装置の場所をマップに表示
端的に言えば、冒頭で述べたデジタルアンドンを具現化することが、スマートメーター用通信ユニットの組立ラインへのMotionBoardの導入目的である。
これまで同ラインでの生産管理は、ほとんどが紙の台帳を起点として行われていた。例えば生産設備に何らかの異常が起きた場合、マニュアルラインでは作業者がボタンを押し、自働化ラインではPLC(Programmable Logic Controller)がアラートを発信し、工場内のモニターにその装置の番号が表示される。それを見たリーダーが現場に駆けつけて対処するが、停止時間や復旧など結果の記録はすべて手書きで行われる。また、同じ台帳に各ラインの生産状況を1時間ごとに記録して予実管理を行うほか、一日の作業終了後にその日の出来高や発生した異常の件数などをまとめて記録し、最終的にPDF化してサーバに保存するという流れだ。
「形の上でこそ電子化されていますが、文書イメージは紙の台帳のままなので、そこから報告書を作成したり、データを分析したりするためには、Excel にデータを再入力して集計やグラフ化などの操作を行う必要があります。また、せっかく長期間にわたって各装置の稼働/ 異常情報を蓄積しているにもかかわらず、特定の故障が過去のどういった経緯から起こる可能性が高いといった傾向を分析することもできず、可動率の改善や予防保守などに活かすことができませんでした」と宇津江氏は振り返る。
これらの課題を解決すべくMotionBoardを活用し、ライン全体をリアルタイムに可視化するダッシュボード、ライン別に単位時間帯ごとや日ごとの出来高推移を可視化するダッシュボードなどが作られた。
「まだ高度な分析や洞察をサポートするところまで至っていませんが、生産活動における様々なKPIをリアルタイムに可視化する機能については、期待にかなり近いレベルで実現できたと思っています。また、従来は製造装置に異常が発生した場合、監視モニターにその装置の番号でしか表示されませんでしたが、MotionBoardのダッシュボードではマップ上に場所を示すことが可能になりました。現場のリーダーからも『よりスムーズに迅速に駆けつけられるようになった』という声が寄せられており、今後に向けてさらなるブラッシュアップを図っていきます」と宇津江氏は語る。
多数のダッシュボードを統括する全社ポータルを用意
先述したようにスマートメーター用通信ユニット組立ラインへのMotionBoard の適用はまだ一部のラインでトライアルを行っている段階だが、すでに公開済みのダッシュボードは確実に生産現場に浸透しており、同社はその実績を踏まえながら対象とするラインや製品、業務を拡大していく考えだ。さらに、今後のダッシュボード開発を加速させるべく、宇津江氏は「すべてを情報システム部門(ビジネスソリューション部)に依存するのではなく、簡単なダッシュボードについては最もニーズがわかっている現場サイドでも開発やカスタマイズができるようにしたいと思います」という意向を示す。
また、同社は部品受入検査やスマートメーター用通信ユニット組立ラインに続き、MotionBoardをベースとした可視化システムの横展開を進めていく計画だ。「その意味でもできるだけ早期に全社ポータルを用意し、その配下で目的別・ライン別のダッシュボードを効果的に運用していくスキームを固めたいと思います」と武井氏は意欲を示す。
生産計画数に対する実績数、各装置の稼働状況、作業の進捗状況、工場経営の意思決定で不可欠なKPI の推移など、同社はあらゆる階層のニーズに応えるデータの可視化を通じて、デジタルで全体最適化された工場のスマート化を推進していく計画だ。
Company Profile
富士通アイ・ネットワークシステムズ株式会社
設立 :1943年(株式会社長谷川電機製作所)
所在地 :山梨県南アルプス市
事業内容 :設計・製造、品質保証、カスタマイズ・サービス
URL :https://www.fujitsu.com/jp/group/finet/
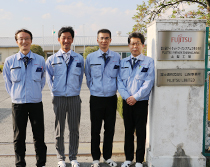
左から
製造統括部 製造部 スマート製造課 課長 宇津江 賢一 氏
ビジネスソリューション部 システム推進 篠原 誠 氏
製造統括部 製造部 部品 担当課長 山口 良和 氏
ビジネスソリューション部 部長 武井 尚也 氏
導入製品
MotionBoard
様々なデータを統合・可視化するBIダッシュボード。統合・可視化にとどまらず、データ入力や柔軟な画面設計で業務に必要なアプリケーションをノーコードで作成可能。