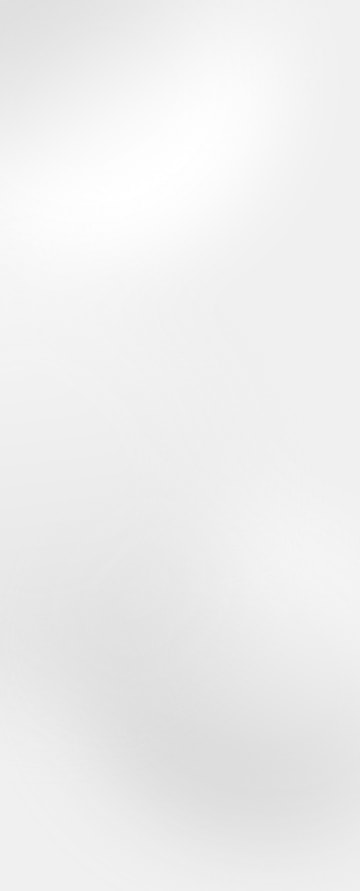
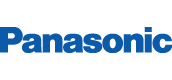
パナソニック株式会社 コネクティッドソリューションズ社
品目マスタ十数万点にも及ぶ部品の中から、意図していない滞留在庫を判別して
スピーディに対応 新たな気づきを職場全体の活動につなげて働き方を変える
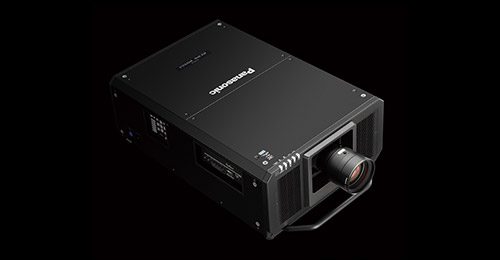
- 業種
-
製造
パナソニック株式会社 コネクティッドソリューションズ社 メディアエンターテインメント事業部 門真工場は、高輝度・高機能の業務用大型プロジェクターの製造を手掛け、グローバル市場でもトップのシェアを有している。だが、そうした中での永遠の経営課題といって過言ではないのが、部品や原材料の滞留在庫の適正化である。その課題解決に向けた新しいツールとして、ウイングアークのDr.SumとMotionBoardで構成された在庫適正化ソリューションを導入。要注意品目の中から意図していない滞留在庫を判別し、迅速な打ち手が可能となった。さらに、正確なデータから新たな気づきを得ることができ、生産現場の働き方そのものも変わってきている。
導入背景
品目マスタで管理されている部品の総数は十数万点にも及ぶ。これをキーとして、生産管理システム(SAP ERP)から必要なデータをAccessで検索し、Excelを用いて集計やグラフ化などを行っているが、データ量が多すぎてPCに取り込めなかったり、処理能力が足りなかったりで、思うように分析できない。また、せっかくレポートを作成しても、その時点ですでに大きなタイムラグが発生しており、最新の生産計画や在庫量などのリアルな数字と乖離しているケースも少なくない。
- 課題
-
- 品目マスタには十数万点もの部品が登録されており、在庫管理で着目すべき品目を絞り込むのが難しい
- 滞留在庫の削減策を導くナレッジが属人化している
- 解決策導入ポイント
-
- 品目ごとの滞留状況をカラーで表現し、要注意品目を浮かび上がらせる
- 滞留在庫の原因を分析し、対応策の検討に必要な情報をダッシュボードに一元化
- 効果
-
- 滞留在庫の課題に気づく“宝探し”がやりやすくなった
- 滞留在庫の金額を工場全体で約15%削減
意図的な滞留在庫と、意図していない滞留在庫を明確に判別した上で、具体的なアクションを導くための気づきを得られるようになった。このデータを正確に伝えることができるので、関係者の理解が進み、職場全体で同じ方向に動けるようになった。また経営層との会議でも、過去の在庫をどうするかという課題について話をするのではなく、未来の適正化や先手の対策に向かっていけるようになった。これにより生産現場の働き方も変わってきた。
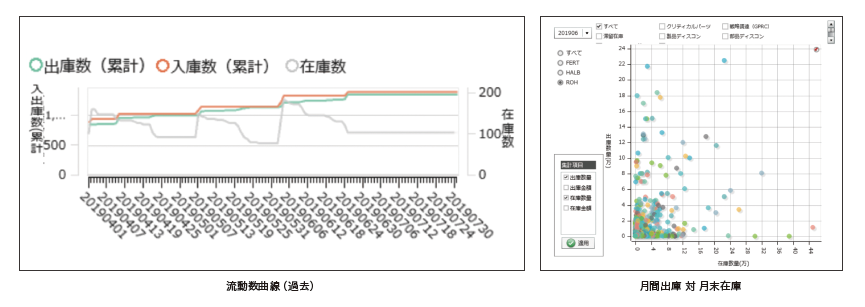
品目マスタに登録された十数万点に及ぶ部品の在庫状況を追いかけるのは至難
あらゆる製造業にとって、部品や原材料の在庫量をいかに適正化するかは、永遠の課題といって過言ではない。経営層にとって在庫の滞留は、資金の滞留そのものを意味している。したがってキャッシュフローやROA(総資産利益率)を高める観点から、できるだけ在庫を減らしたいと考える。
一方で生産現場では、「サプライヤーからの納品が遅れるかもしれない」「工程が遅れるかもしれない」「営業部門から特急オーダーがくるかもしれない」など、将来に対する様々な不確実性を抱えている。顧客の希望納期に応えて機会損失を防ぐために、どうしても在庫は増えていく傾向が強い。
様々なホールや施設、あるいは屋内外のイベント会場でのプロジェクションマッピングなどで用いられる業務用大型プロジェクターの製造を手掛けているパナソニックメディアエンターテインメント事業部の門真工場も例外ではなく、同じ悩みを抱えている。
同事業部門真工場 生産管理課で課長を務める坂口 豊隆氏は、「高輝度・高機能の大型プロジェクターに関してグルーバル市場でもトップのシェアを有しており、高い品質と革新的な技術は、世界的なデザイン賞やメディアから高く評価されています」と紹介する。
それだけにモノづくりの工程も複雑だ。同社のプロジェクターは、パナソニック独自のレーザーテクノロジーや4K映像投射、デジタルリンクなどの機能に対応したハイテクのかたまりでもあり、用いられている部品の品目は約1万点強に上る。「一つひとつの品目の在庫の動きを人の目で追いかけ、管理するのは至難の業です」と坂口氏は語る。
実際、在庫管理の現場ではどんな苦労が発生しているのだろうか。同課の伊藤 里佳氏は、このように語る。
「実際に在庫が存在する部品は約1万点強ですが、品目マスタで管理されている部品の総数は十数万点にも及びます。これをキーとして、生産管理システム(SAP ERP)から必要なデータをAccessで検索し、Excelを用いて集計やグラフ化などを行っているのですが、とにかくデータ量が多すぎてPCに取り込めなかったり、処理能力が足りなかったりで、思うように分析できないことが多々ありました。また、せっかくレポートを作成しても、その時点ですでに大きなタイムラグが発生しており、最新の生産計画や在庫量などのリアルな数字と乖離しているケースも少なくありません」
また、部品ごとに異なる納期のリードタイムやMOQ(最低発注数量)のサイズも在庫管理を複雑化させる要因となっている。要するに各部品について、在庫量が一定のしきい値を下回ったら発注をかけるといった単純なアクションを実行するだけでは、適正な在庫量を維持することはできないのだ。
同課の高木 紀広氏は、「例えば、生産中止が決まった製品で使われているMOQサイズの大きな部品については、サプライヤーに対して最終発注のMOQを下げてもらう交渉が必須となります」と語る。このアクションが遅れた場合、サービス品(保守部品)として確保しておくべき数量を大幅に上回る在庫を積み残してしまうことにもなりかねないのだ。
在庫管理の高度化を目標としたツール活用の2つの方向性
在庫管理の困難に対して、同門真工場がこれまで基本としてきたのは、特に高価格帯の部品の在庫を集中的にコントロールするという方法である。というより、今まではそうした限定的なアプローチしかできなかったのが率直なところだ。そしてこの限界を超えて在庫管理の高度化を図るべく、同事業部が目指したのが次のようなツール活用の方向性である。
①滞留在庫が引き起こす様な課題の発見(宝探し)
在庫を「カネ」だけではなく「モノ」として見た場合にも、保管コストや荷役コスト、廃棄コストの増大、サービスレベルの低下など、様々な課題がある。「仮に部品の単価は安くて過剰在庫がそれほど大きな経営上の負担にならなかったとしても、荷姿が大きく保管庫があふれて生産活動に支障をきたす場合もあります。こうした今まで気づいていなかった課題を発見することは、まさに生産活動における“宝探し”であり、在庫管理の改善や高度化に向けた最大の目的としました」(坂口氏)
これを実現するためには、多岐にわたるKPI(重要評価指標)を可視化して課題に対する多角的な気づきを与え、生産現場にアクションを促すツールが必要となる。
②リアクティブな在庫管理からプロアクティブな在庫適正化への転換主要な部品の中には納品までに半年以上
主要な部品の中には納品までに半年以上のリードタイムを要するものも多いことから、ルーティンで発注を行うとどんどん在庫が積み上がってしまう。そうした中で現時点の在庫を捉え、それをどう消費するかという観点から対策を練っていた。「今後はそうした後追い型の管理ではなく、最初から『余分なものを買わないためにツールを使う』という先手管理を徹底させなければなりません」(坂口氏)
製造現場の“モヤモヤ”を、可視化可能なテキストや数値で表現
では、具体的にどんなツールを活用することで、上記の目標実現に向けた在庫管理の改善を進めていくのか−−。検討を重ねた結果、同工場が採用したのが、ウイングアークの在庫適正化ソリューションである。Dr.SumおよびMotionBoardで構成され、「在庫削減すべき対象品目を絞り込む「在庫削減の方策を立て、実施する」「在庫削減の効果測定をする」といった一連のステップの実行をサポートするものだ。
実は同工場はすでにMotionBoardを導入しており、情報企画部門の協力のもと、各種経営情報の可視化や分析に活用していた。そこにウイングアークから「こんな用途にもダッシュボードを使えます」と、在庫適正化のテンプレートを提示されたことが、このソリューションの導入に至ったきっかけである。同工場 製造企画課 主幹の山中 崇博氏は、こんなエピソードを明かす。
「MotionBoardを在庫管理にも使いたいという思いは以前からあったのですが、製造現場から上がってくる様々な課題や要望を、正しく理解し、定義することから大きな困難がありました。その “モヤモヤ”を可視化可能なテキストや数値で表現すべく、BI ツールやデータ分析に精通した情報企画部門のスタッフが通訳のような役割を果たしてくれました。情報企画部門のスタッフとウイングアークのコンサルタントは数回にわたる方針のすり合わせを実施。さらに、両者は製造現場に足を運び、その“モヤモヤ”とした要望をその場でテンプレートに組み込んで可視化し、修正を繰り返しながら、ギャップを埋めていった。「あたかもアジャイル開発のような感覚で試行錯誤しながらダッシュボードをカスタマイズしている姿を目のあたりにして、これならば在庫に関する様々な課題を必ず解決できると確信しました」と山中氏は語る。
新たな気づきが職場全体の活動につながり、働き方を変えていく
こうして同工場は2019年3月末、生産管理システムで管理されている在庫情報を転送して時系列で蓄積するデータウェアハウスとなるDr.Sumと共に、在庫適正化ソリューションを正式導入。標準テンプレートとして提供されたダッシュボードのカスタマイズを進めつつ、同年4月より“走りながら考える”スタイルで実業務での運用を開始した。
そこでは具体的にどんな活用がされているのか。ダッシュボードには主要製品の部品在庫の滞留状況が金額(単価×数量)の高い品目順にカラーで表示される。さらに、そこから浮かび上がってきた要注意品目について、ロケーション別にドリルダウンしてその内訳を見たり、流動数曲線※ 1を用いて過去の滞留状況の傾向を調べたり、今後の入出庫予定を確認できるという仕組みだ。
「在庫は必ずしも悪じゃない」と強調する伊藤氏の言葉を受けつつ、同事業部の納谷 裕美子氏は、「このダッシュボードができたことで意図的な滞留在庫と、意図していない滞留在庫を明確に判別した上で、具体的なアクションを導くための気づきを得られるようになりました」と語る。
例えば、MOQサイズの大きな部品は、どうしても入庫のたびに一時的に滞留在庫が跳ね上がる。また、主要製品の重要部品について、納期に余裕をもたせるためにあえて大量の在庫を確保している場合もある。こうした意図的な滞留在庫は、近々の消費が見えているならまったく問題はない。だが、単に欠品をおそれて余裕を持ち過ぎていたり、製造中止部品だったりした場合は大きな問題となる。こうした個々の状況に応じた的確な手を迅速に打てるようになったのである。
また、この結果として「滞留在庫の金額を工場全体で15%程度削減できています」と坂口氏は強調する。
それだけではない。「データを正確に伝えることができるので、関係者の理解が進み、職場全体で同じ方向に動けるようになりました。また経営層との会議でも、過去の在庫をどうするかという課題について話をするのではなく、未来の適正化や先手の対策に向かっていけるようになりました」
「ツールを通じて業務上の様々なことに気づくことができ、まだ使い始めて2ヶ月ほどですが生産現場の働き方も変わってきています(坂口氏)」
もっとも、先に述べた「滞留在庫が引き起こす多様な課題の発見」や「プロアクティブな在庫適正化への転換」といった目標からすれば、現状のダッシュボードはまだ途中過程にあり、さらなるカスタマイズと機能強化が求められる。
「そのためにも在庫をもっと多角的に捉える必要がありますが、机上でデータを眺めているだけでは新たな気づきを得ることはできません。そこで在庫適正化ソリューションの導入前に行ったのと同じように、私もPCを持参して、各製造ラインを回っています。現場の人たちとダッシュボードを一緒に見ながらその場の状況を確認したり、意見を聞いたり、直接コミュニケーションを取ることで課題や要望を洗い出しています」と伊藤氏は語る。こうして得られた新たな気づきや知見を、在庫適正化ソリューションの今後の機能に反映していく考えだ。
もう1つのテーマとして浮上しているのは、人に依存している判断の自動化だ。「例えば、流動数曲線から過去の滞留在庫の傾向を読み取るには相当な熟練が必要とされますが、そこには在庫が滞留しやすいパターン、あるいは在庫が不足しがちなパターンなどが隠れています。これらのパターンをAI技術などで学習できれば、先手を打ってアラートを出すことが可能になるのではないかと考えています」と坂口氏は語る。
同事業部は今後もウイングアークとの緊密な交流のもと、在庫適正化ソリューションのブラッシュアップを図っていく計画だ。
※1 入庫数と出庫数それぞれを、縦軸を累積数、横軸を日付としてグラフ化することで、入出庫のコントロール状況を確認。二つの線が上下に離れるほど余剰在庫の増加、左右に離れるほど滞留期間の増加を表す。
Company Profile
パナソニック株式会社 コネクティッドソリューションズ社
本社所在地 :東京都中央区
事業内容 :「航空」「製造」「エンターテインメント」「流通」「物流」「パブリック(公共)」分野向け機器の開発/製造/販売ならびに、システムインテグレーション/施工/保守・メンテナンス、及び、サービスを含むソリューションの提供
URL :https://www.panasonic.com/jp/corporate/cns.html
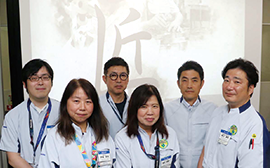
パナソニック株式会社 コネクティッドソリューションズ社
メディアエンターテインメント事業部 マニュファクチャリングセンター 門真工場
(前列左から)
生産管理課 伊藤 里佳氏
生産管理課 納谷 裕美子氏
生産管理課 課長 坂口 豊隆氏
(後列左から)
生産技術課 主務 尾原 礼俊氏
生産管理課 主務 高木 紀広氏
製造企画課 主幹 山中 崇博氏
導入製品
MotionBoard
様々なデータを統合・可視化するBIダッシュボード。統合・可視化にとどまらず、データ入力や柔軟な画面設計で業務に必要なアプリケーションをノーコードで作成可能。
Dr.Sum
あらゆるデータをリアルタイムに収集・蓄積・分析する、データベースエンジンを軸としたデータ分析基盤。10億件のデータも1秒台で集計する超高速集計を実現。