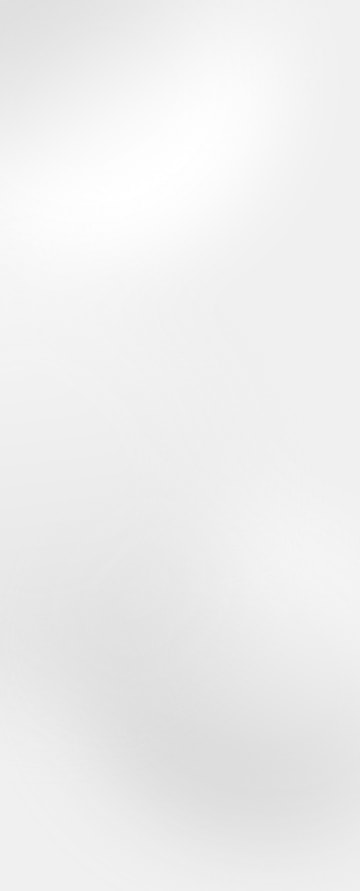
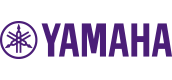
ヤマハ株式会社
データドリブンで進む生産プロセスの改善とデジタルツイン化
スマートファクトリーの取り組みをMotionBoardが支える
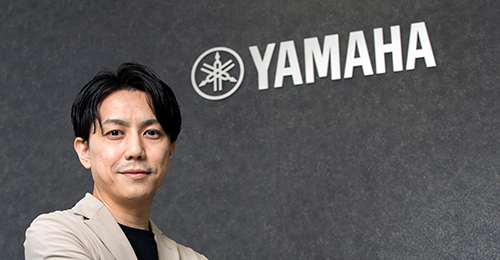
- 製品
- 業種
-
製造
楽器・音響メーカーとして世界をリードするヤマハ株式会社(以下、ヤマハ)は、中期経営計画「MAKE WAVES 2.0」を“成長力を高める”フェーズと位置付け、これを実現すべく、楽器工場のスマートファクトリー化に注力している。これまでにサックスの組立工程においてIoT活用による生産効率化を達成し、現在はギターの組立工程においてデジタルツインを活用したリモート生産管理のPoC(概念実証)を実施。それらの取り組みを支えるツールとして「MotionBoard」を採用し、データのモニタリングやシミュレーション、現場でのアジャイルな業務改善を進めている。
導入背景
これまで、世界13ヶ所の工場や各楽器製造ラインが独自にIT化、IoT化を進めてきたため、システムがサイロ化し、全社的なデータ活用ができていなかった。そこで、全社横断でのスマートファクトリー化を進めるべく、楽器工場内の生産の効率化(=プロセス改善)と、全社的な生産工場のリモート管理(=プロセスチェンジ)に挑戦し、それを支える仕組みとして製造現場でもすぐに活用できるダッシュボードの導入を検討していた。
- 課題
-
- メーカーとして、QCD(品質・コスト・納期)+SE(安全・環境)を継続的に向上させたい
- 経験値や勘コツ、現場へのヒアリングによる現場管理で生じる製造プロセス・生産数のばらつきを是正したい
- 国内外に点在する生産工場の管理を遠隔からスムーズに行いたい
- 競争力の源泉であるクラフトマンシップ(匠の技)を適切に継承させて人材育成を効率化したい
- 解決策導入ポイント
-
- IoT(ビーコン)デバイスとカメラでデータを取得し、ダッシュボードや“あんどん”を活用した実績管理・進捗管理の仕組みを導入
- 国内、海外の全工場の製造プロセス統一のために、部品表(BOM)に工程設計情報等を統合したBOP(Bill of Process)を構築
- BOPに基づいてIoTデバイスで実績データを収集し可視化することでデジタルツインを実現し、それを活用したリモート生産管理の仕組みを検証し確立
- 効果
-
- データに基づいた現場のコントロールと生産管理により、半年でサックスの生産能率が16%向上
- 楽器工場内で働くクラフトマンたちの意識改革を実現
- BOP整備による楽器製造プロセス標準化活動を牽引
柔軟さと強靭さを備えた企業を目指しスマートファクトリーを推進
世界的な楽器・音響メーカーであるヤマハは、先人から受け継いだ匠の技と長年培ってきたブランド力で、長きにわたり市場を牽引してきた。昨今のコロナ禍においても、楽器や音響製品の巣ごもり需要などがあり、事業は堅調に推移している。一方で同社では、継続的な成長を見据え、2022年度から3ヶ年の中期経営計画「Make W aves 2.0」において、事業基盤を強化する方針の中で「柔軟さと強靭さを備え持つ」という重点テーマを掲げ、生産・技術開発の高度化を実現するためのスマートファクトリー化に取り組んでいる。
ヤマハが工場のスマート化を進める背景にあるのが、新興国をはじめとする海外メーカーとの競争である。楽器・音響生産本部 生産企画統括部 企画推進部 スマートファクトリー推進グループ リーダーの宮田 智史氏は、ヤマハが置かれている楽器製造の市場環境について次のように説明する。
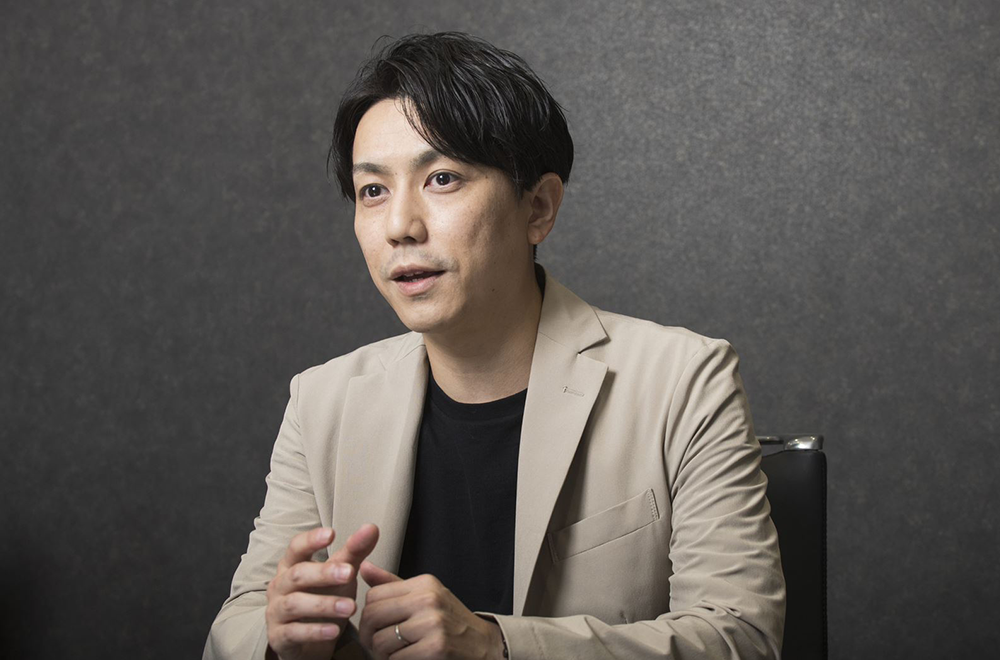
「世界で台頭しつつある新興勢力との競争に勝ち残っていくためには、工場のQCD+SE(品質、コスト、納期+安全、環境)の管理を強化して顧客提供価値を上げていく必要があります。特に昨今では、コロナ禍の影響、半導体不足、木材価格の高騰でサプライチェーンも混乱しており、生産領域においてスマートファクトリー化やDXによって柔軟さと強靭さを備えていくことが、ポストコロナの世界で事業基盤を強化していくうえで必須なのです」(宮田氏)
現場でも簡単に使える操作性とイニシャルコストを評価しMotionBoardを採用
スマートファクトリー化を推し進める前にも、ヤマハでは2010年代から工場内のIT化やIoT化を進めてきた。ただし国内外13ヶ所の各工場が独自に取り組んでいたため、システムのサイロ化が生じていた。「その結果、取得するデータやデータの取り方そのものが異なってしまい、IT化が進んでも全社的なデータ活用は実施できずにいました」(宮田氏)
そこで各工場を横串で管理するとともに、データ管理の標準化を実現するために、2018年にスマートファクトリー推進グループを発足し、全社でのスマートファクトリー化に着手した。同グループではこれまでに、「サックス組立工程でのIoT(ビーコン)を活用した実績管理」と、「ギター組立工程におけるデジタルツインPoC」という2つの先進的な取り組みを実施。前者は生産性の向上を目的とし、後者は製造DXの一環としてデジタルツインによるリモート生産管理の可能性を検証するものであり、それぞれの取り組みにMotionBoardが活用されている。
ヤマハが初めてMotionBoardを導入したのは、同製品がリリースされて間もない2012年のことだ。ヤマハ豊岡工場において電子基板実装工程と電子楽器組立工程を可視化する生産管理システムとして成果をあげ、その評判が工場内で広がり、管楽器(リコーダー)の成型工程、ピアノの塗装工程などで導入が進んでいった。当時豊岡工場に在籍していた宮田氏は、導入の経緯と活用状況について次のように語る。
「他社のBIツールも検討しましたが、利用の際にコーディングが前提となる製品がほとんどだったため、工場で活用するにはハードルが高く導入を断念しました。MotionBoardには、ノーコードでダッシュボードを構築できること、手頃な価格で利用できることなどが決め手となり、導入に至りました。導入後にすぐに効果が発揮され、その評判を聞いた工場内の他の製造ラインで自発的に採用が広がり、今では多くの楽器製造工程で欠かせないツールになっています」(宮田氏)
サックス組立工程のプロセス改善により生産性が16%向上
宮田氏は、2018年10月のスマートファクトリー推進グループ創設に伴い、同グループに異動。2013年迄は工場側で生産効率化を推進する立場だったが、新たに本社側のDX推進担当者として、MotionBoardを活用したスマートファクトリー化の取り組みに参画することになった。
スマートファクトリー推進グループが最初に取り組んだのが、サックス組立工程におけるビーコンを活用した実績管理システムの構築だ。同システムを導入し、人やモノの動きが不規則な約30人のラインで、組立中のサックスにビーコンを付けて作業中の軌跡を追えるようにした。ビーコンの他にも、作業の様子がIPカメラで録画され、それらのデータが独自開発のデータ統合基盤である「IoTプラットフォーム」に送信されて、可視化される仕組みとなっている。
その結果、どの作業にどれだけ時間がかかっているか、滞留しているエリアや作業が遅い工程などを現場の管理者がダッシュボードを使って把握できるようになり、その要因をドリルダウンして分析できるようになった。経験値や勘コツ、ヒアリングによる現場コントロールからデータドリブンのコントロールに変わり、2020年5月に稼働後、わずか半年で “稼ぎ頭”であるサックス組立工程の生産性が16%向上した。
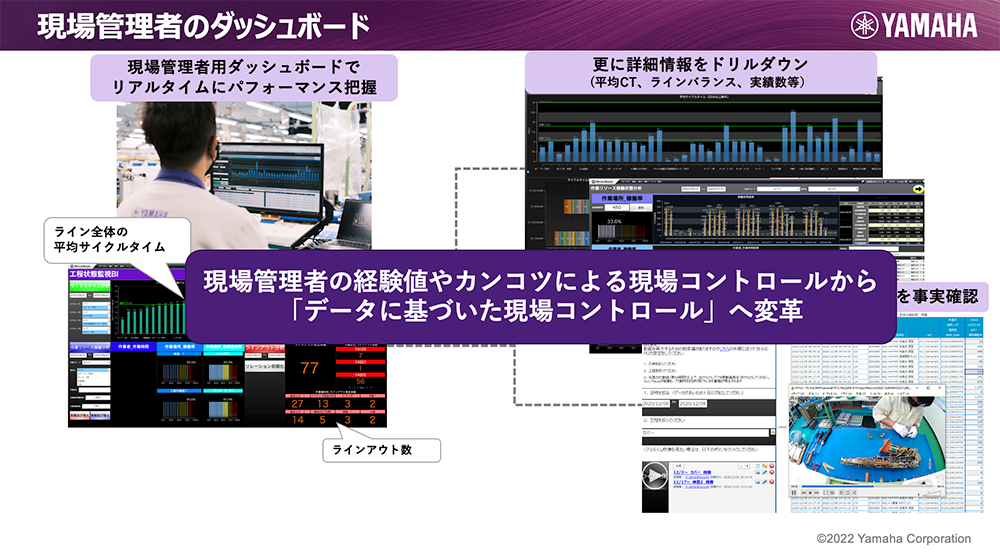
また蓄積された情報は、工場内のあんどん(生産ラインを効率的に管理する仕組み)や手元のタブレットにも表示される仕組みとなっている。これにより、従来であれば30人が安定した作業をしないと高いアウトプットを出せない中で、作業者のペースメイキングが安定した。ラインバランスが20%向上するとともに、現場が助け合ったりデジタルを活用した業務改善を提案したりするようになったという。
「ダッシュボード開発は内製していますが、MotionBoardに初めて触れた推進グループのメンバーでも簡単に開発することができました。週に一度、現場管理者と推進メンバーで開催している現場改善会の場では、会議室でダッシュボード画面のデータや動画を見ながら事実ベースで討論でき、データに基づいて症状確認し、改善のための意思決定ができています。今はメンテナンスや改善に向けた開発も工場側に委ね、完全に自走しています」(宮田氏)
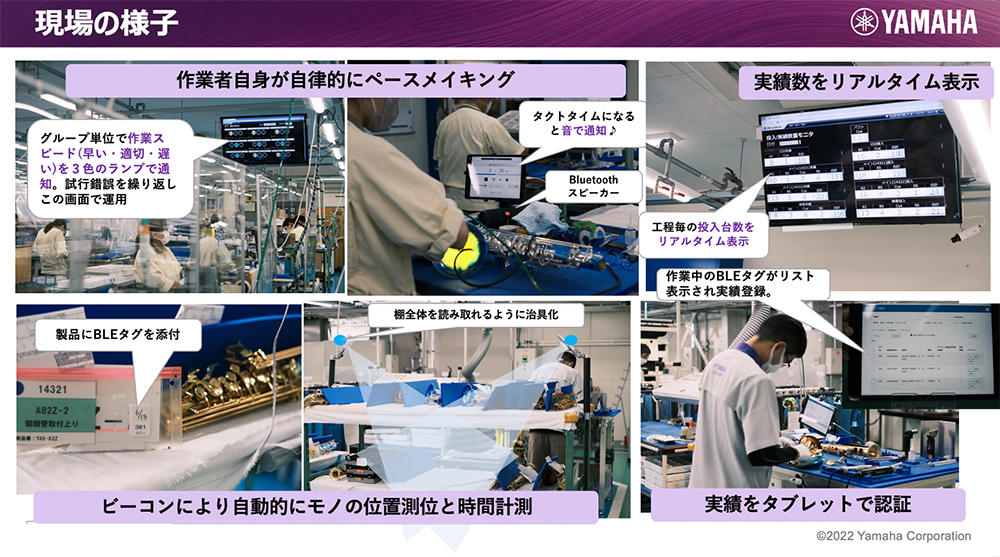
ヤマハ標準モデルを活用したデジタルツインを確立
そして現在取り組んでいるのが、ギター組立工程におけるデジタルツインの概念実証である。サックス組立工程の取り組みが生産性向上を目的としたものであるのに対し、こちらは各工場の生産管理DXを実現するために、実際の工場からデータを収集し、デジタル空間上に再現する“デジタルツイン”の仕組み自体に効果があるかを検証する取り組みである。
「今回の取り組みで、デジタルツインの概念がヤマハの工場において成立するか、DXが起こりうるかを判断します。最初の目標は、生産管理を遠隔で行えるようにし、生産管理業務をDXすることです。第1段階は『データによる工場管理ができる状態にする』、第2段階は『現場に赴かなくてもデータにより工場内外から必要な対応や支援をタイムリーに行う』という1つの可能性を検証しています」(宮田氏)
デジタルツインの構築に先駆けてヤマハでは、各工場の製造プロセスを統一するために、部品表(BOM)に工程設計情報等を統合した「ヤマハ製造モデル」という概念を定義し、BOP(Bill of Process)、BOR(Bill of Resource)の構築を進めている。今回のデジタルツイン構築のタイミングで、ギター組立工程において初めてヤマハ製造モデルに準ずるモデルを開発した。
デジタルツインの構成は、下の図の通りだ。まず実際の工場から「プロセスの時間」「作業の時間」「モノの数・位置」「モノの投入履歴」「作業リソースの投入時間」「作業リソースの作業条件」という6つのデータをQRコード、RFID、ビーコン、IPカメラおよびタブレットへの入力等のIoTデバイスを通じて吸い上げる。ギター組立用製造モデルで定義したプロセスでその都度発生したデータは「IoTプラットフォーム」「MES」「ERP」という3層からなるデータ統合基盤に送られ、それらのデータを基にデジタル空間上に、仮想工場のデジタルツインを再現する仕組みとなっている。デジタルツインはMotionBoardによって可視化され、ダッシュボードを通じて管理者や改善の担当者がモニタリング、分析を行い、遠隔からデータを見て現場に指示が出せる形となっている。
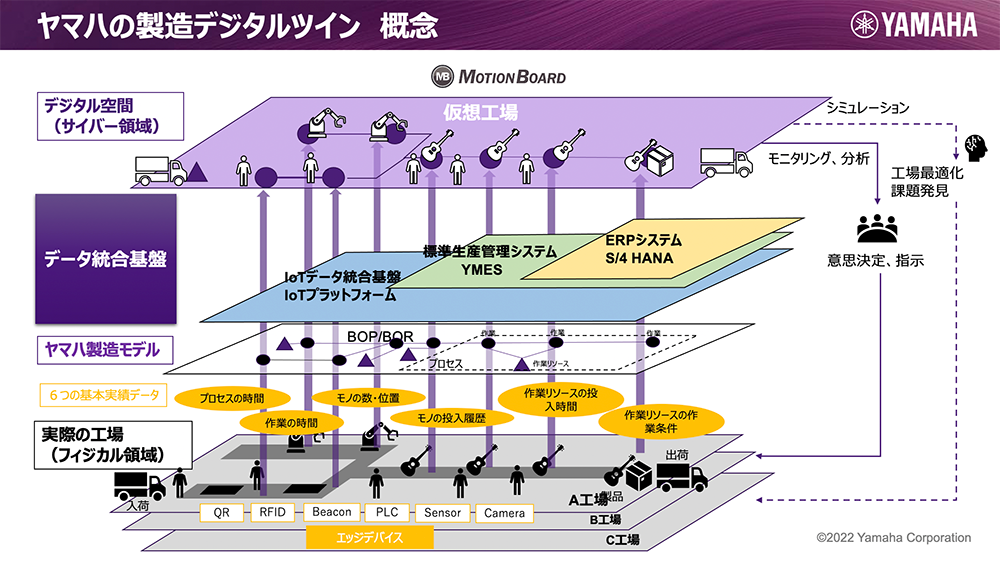
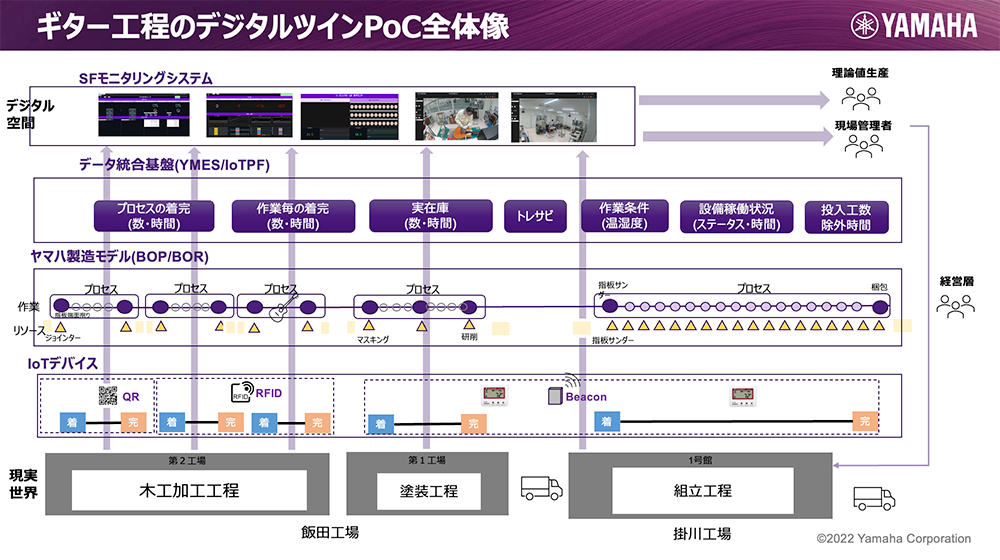
デジタルツインの開発にあたっては、ウイングアークの担当者の意見も参考にした。
「ウイングアークはツールを売るだけでなく、製造業におけるデータ活用のノウハウがあります。他社の活用例やニーズを押さえたうえで最適な提案をしてくれます。リモート生産管理の仕組みやデジタルツインのダッシュボードを開発した際も、第三者視点からのアドバイスがとても役に立ちました。また、MotionBoardには、開発に必要な機能が全て揃っているため、情報を置くだけでなく映像連携も可能です。この仕組みの作成を外部に依頼するとなると数百万円かかってしまうため、自分たちだけで作り込める点は大きなメリットです」(宮田氏)
続けて、操作性について宮田氏は、「ビジュアルも単純に数字を出すだけでなく、アイキャッチできるオブジェクトが揃い、アラートで発信できるバリエーションも多く、3Dマップを見てもらうための動機作りに役立つさまざまな要素が入っていて使いやすいですね。そこは国産製品ならではの強みだと感じます」と高く評価する。
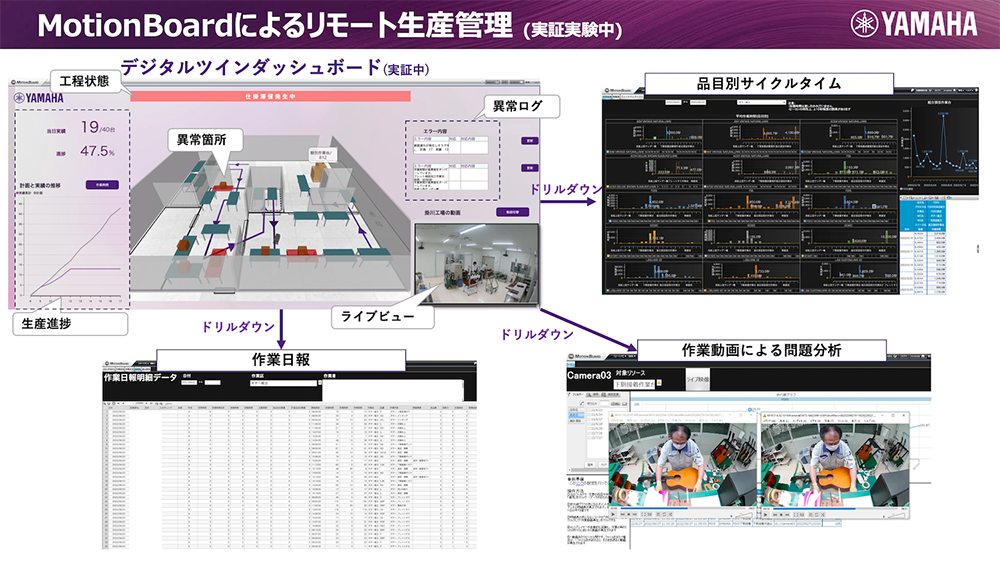
製品を軸としたデジタルツインの国内普及に期待
ヤマハでは今後、デジタルツインによって各工場を遠隔かつ横断的に状況確認し、データドリブンで意思決定して問題解決できる仕組みを構築しようとしている。また、さらなるデジタル活用により生産領域を自動化していく計画も考えているとのこと。「暗黙知など職人技自体に価値がある領域については手を加えず、反対に管理領域などテクノロジーで効率化できるものについては積極的に変えていく方針です。この2つの領域を見極めながら工場のDXを進めていきます」と宮田氏は今後を展望する。
その中で、ウイングアークに対する期待も大きい。ヤマハはMotionBoardの10年来のユーザーであり、同社の要望に沿って製造業に必要な多くの機能を実装してきたという経緯もある。そして新たに宮田氏は、期待する領域として動画まわりの進化を挙げる。
「製造業では『現場・現物・現実』の3現主義で、モノを確認して事実で判断するのが常識ですが、リモート生産管理やデジタルツインは、それと真逆のものです。そこでは、必ず動画活用のニーズが高まっていくでしょう。今後は動画のストリーミングやAIを活用した異常検知機能などが備わり、プログラミングレスで実装できるようになることを期待しています」(宮田氏)
これまでヤマハは、MotionBoardを通じて現場がITを活用するという国内製造業の成功例を作ってきた。今後スマートファクトリー領域でもリモート管理の技術を確立し、日本の製造業を牽引していく存在になっていくことだろう。
Company Profile
ヤマハ株式会社
創業:1887年(明治20年)
所在地:静岡県浜松市
事業内容:ピアノ、電子楽器、管・弦・打楽器等の製造販売等を担う楽器事業、オーディオ、業務用音響機器、情報通信機器等の製造販売を行う音響機器事業の2つを中核事業として展開。また、電子部品事業、自動車用内装部品事業、FA機器事業、ゴルフ用品事業、リゾート事業等も手掛けている。
URL:https://www.yamaha.com/ja/
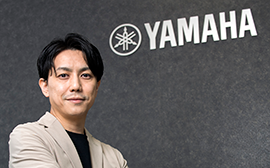
楽器・音響生産本部 生産企画統括部
企画推進部 スマートファクトリー推進グループ
リーダー 宮田 智史氏
導入製品
MotionBoard
様々なデータを統合・可視化するBIダッシュボード。統合・可視化にとどまらず、データ入力や柔軟な画面設計で業務に必要なアプリケーションをノーコードで作成可能。